In the ever-evolving world of textiles, innovation is key to staying ahead. Textile companies that embrace cutting-edge technologies and sustainable practices are leading the way in textile-cutting solutions. Here are ten reasons why these innovative textile companies are at the forefront of the industry.
1. Advanced Cutting Technologies
Innovative textile companies invest in the latest cutting technologies, such as laser cutting and ultrasonic cutting. These methods offer precision and efficiency, reducing waste and improving the quality of the final product. Laser cutting, for example, allows for intricate designs and clean edges, which are essential for high-quality textiles.
2. Automation and Robotics
Automation and robotics have revolutionized the textile industry. Automated cutting machines can work around the clock, increasing productivity and reducing labor costs. Robotics also ensure consistent quality and precision, which is crucial for maintaining high standards in textile production.
3. Sustainable Practices
Sustainability is a major focus for leading textile companies. They adopt eco-friendly cutting methods that minimize waste and reduce energy consumption. For instance, waterjet cutting uses a high-pressure stream of water to cut textiles, which is both efficient and environmentally friendly.
4. Customization and Flexibility
Innovative textile companies offer customization options to meet the specific needs of their clients. Advanced cutting technologies enable these companies to produce bespoke designs and tailor-made solutions. This flexibility is a significant advantage in a competitive market.
5. Integration of Smart Technologies
The integration of smart technologies, such as IoT and AI, has transformed textile cutting solutions. These technologies enable real-time monitoring and optimization of the cutting process, leading to increased efficiency and reduced downtime. Smart sensors can detect and correct errors, ensuring high-quality output.
6. High-Speed Cutting
Speed is a critical factor in textile production. Leading textile companies use high-speed cutting machines that can handle large volumes of fabric quickly and accurately. This capability is essential for meeting tight deadlines and maintaining a competitive edge.
7. Precision and Accuracy
Precision and accuracy are paramount in textile cutting. Innovative companies use advanced software and cutting tools to achieve precise cuts, reducing material waste and ensuring consistent quality. This attention to detail is what sets them apart from the competition.
8. Cost-Effective Solutions
By adopting advanced cutting technologies and automation, textile companies can reduce production costs. These cost savings can be passed on to customers, making high-quality textiles more affordable. Additionally, efficient cutting processes minimize waste, further reducing costs.
9. Enhanced Safety Measures
Safety is a top priority for leading textile companies. They implement advanced safety features in their cutting machines to protect workers and prevent accidents. For example, laser cutting machines are equipped with safety sensors that automatically shut down the machine if a hazard is detected.
10. Continuous Innovation
The most successful textile companies are those that continuously innovate. They invest in research and development to stay ahead of industry trends and adopt new technologies. This commitment to innovation ensures they remain leaders in textile-cutting solutions.
One such example of continuous innovation is the Svegea CMS 1800A2 Strip Cutter. This versatile machine is renowned for its precision in cutting various types of fabrics into strips, making it ideal for producing bias binding, piping, and other narrow fabric applications. The CMS 1800A2 Strip Cutter exemplifies the advanced cutting technologies and efficiency that set leading textile companies apart.
Innovation At Its Finest
Innovative textile companies are leading the way in textile-cutting solutions by embracing advanced technologies, sustainable practices, and continuous innovation. These companies set the standard for quality, efficiency, and customization in the textile industry. If you’re looking for cutting-edge textile solutions, consider exploring the products offered by Svegea of Sweden. Visit our product page to learn more about our innovative textile-cutting solutions.
In today’s world, sustainability is more than just a buzzword; it’s necessary. The textile industry, known for its significant environmental impact, is transforming greener practices. Central to this shift is the adoption of sustainable textile production methods. The importance of using the right equipment lies at the heart of these methods. This blog will explore how advanced machinery contributes to a greener future and why choosing the right equipment is crucial for sustainable textile production.
The Environmental Impact of Textile Production
Textile production is one of the most resource-intensive industries globally. It involves the extensive use of water, energy, and chemicals, leading to significant environmental pollution. Traditional textile manufacturing processes often result in high levels of waste and emissions, contributing to water and air pollution. However, with the right equipment, these negative impacts can be significantly reduced.
Advanced Machinery: The Key to Sustainable Textile Production
Modern textile machinery is designed with sustainability in mind. These machines are more efficient, consume less energy, and produce less waste. For instance, advanced dyeing machines use less water and chemicals, reducing the environmental footprint of the dyeing process. Similarly, automated cutting machines minimize fabric waste, ensuring that every piece of material is utilized effectively.
One of the leading companies in this field is Svegea of Sweden. Their innovative machines are at the forefront of sustainable textile production. By integrating advanced technology and sustainable practices, Svegea’s equipment helps manufacturers reduce their environmental impact while maintaining high production standards. For more information on sustainable textile and leather production standards, you can visit the OEKO-TEX® STeP certification page.
Benefits of Using Sustainable Textile Machinery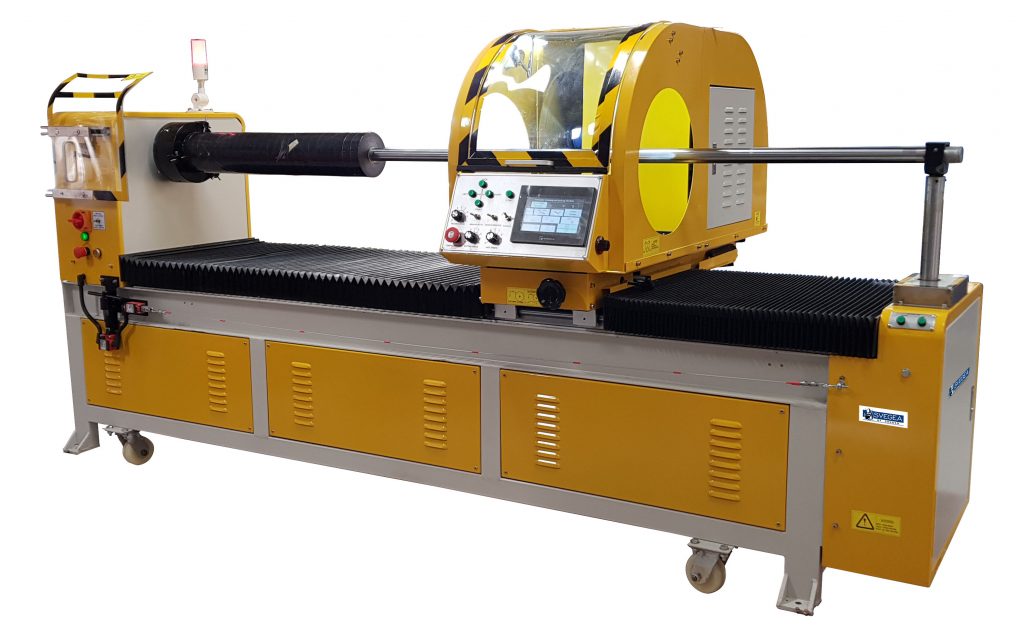
1. Reduced Energy Consumption: Modern textile machines are designed to be energy-efficient. They use advanced technologies such as variable frequency drives and energy recovery systems to minimize energy usage. This not only reduces the carbon footprint but also lowers operational costs.
2. Water Conservation: Traditional textile production processes are notorious for their high water consumption. Advanced machines, however, use water more efficiently. For example, modern dyeing machines can recycle water, significantly reducing the amount needed for each cycle.
3. Minimized Chemical Use: Sustainable textile machinery is designed to use fewer chemicals. This is achieved through precise control systems that ensure optimal use of dyes and other chemicals, reducing waste and environmental contamination.
4. Waste Reduction: Automated cutting and sewing machines are programmed to maximize fabric usage, reducing waste. This not only conserves resources but also lowers disposal costs.
5. Improved Product Quality: Sustainable machines often produce higher-quality textiles. This is because they operate with greater precision and consistency, leading to fewer defects and higher overall product quality.
The Future of Textile Production
The future of textile production lies in sustainability. As consumers become more environmentally conscious, the demand for sustainably produced textiles will continue to grow. Manufacturers who invest in the right equipment will be better positioned to meet this demand and stay competitive in the market.
Moreover, regulatory pressures are increasing, with governments around the world implementing stricter environmental standards. By adopting sustainable textile production practices now, manufacturers can stay ahead of these regulations and avoid potential penalties. For a deeper dive into sustainable textiles, you can read this blog post on eco-friendly fabric production.
Starting with the Right Equipment
Sustainable textile production starts with the right equipment. Advanced machinery not only reduces the environmental impact of textile manufacturing but also offers numerous benefits such as lower energy consumption, water conservation, minimized chemical use, waste reduction, and improved product quality. Companies like Svegea of Sweden are leading the way with their innovative and sustainable machines.
At Svegea of Sweden, we pride ourselves on leading the way in sustainable textile production. Our machines are designed to be both efficient and environmentally friendly. For instance, our automatic collarette cutting machines are renowned for their precision and minimal waste production. By investing in such advanced equipment, we help textile manufacturers significantly reduce their environmental impact.
Our commitment to sustainability extends beyond our products. We also focus on sustainable practices within our operations, such as using renewable energy sources and implementing waste reduction programs. This holistic approach ensures that our contribution to a greener future is comprehensive and impactful. To learn more about how advanced textiles are being developed to improve performance and sustainability, check out this article from Textile World.
If you’re looking to make your textile production more sustainable, consider investing in advanced machinery from Svegea of Sweden. Their commitment to sustainability and cutting-edge technology can help you achieve your environmental goals while maintaining high production standards.
Contact Svegea of Sweden today to learn more about how their machines can contribute to a greener future for your textile production.
In the ever-evolving textile industry, fabric inspection has always been a critical yet challenging task. Ensuring the highest quality of fabrics is essential for maintaining brand reputation and customer satisfaction. However, traditional methods of fabric inspection are often time-consuming and prone to human error. This is where artificial intelligence (AI) steps in, revolutionizing the way we approach fabric inspection.
The Need for Advanced Fabric Inspection
As someone deeply involved in the textile industry, I have witnessed firsthand the limitations of manual fabric inspection. The process is labor-intensive and can miss subtle defects that affect the final product’s quality. With the increasing demand for flawless fabrics, there is a pressing need for more efficient and accurate inspection methods.
How AI Transforms Fabric Inspection
AI technology has brought a significant shift in fabric inspection processes. By integrating AI, companies like Svegea of Sweden are setting new standards in quality control. AI systems use high-resolution cameras and sophisticated algorithms to detect defects that human eyes might overlook. These systems can identify issues such as misweaves, pattern irregularities, and color deviations with remarkable precision.
One of the most impressive aspects of AI in fabric inspection is its ability to process vast amounts of fabric quickly. What used to take hours can now be done in minutes, significantly speeding up the production cycle and reducing labor costs. This efficiency not only enhances productivity but also ensures that only top-quality fabrics reach the market.
Svegea of Sweden: Leading the Way
Svegea of Sweden has been at the forefront of integrating AI into fabric inspection. Their innovative approach combines advanced technology with industry expertise to deliver unparalleled results. For instance, their latest fabric inspection machine, equipped with AI capabilities, can scan and analyze fabrics in real-time, ensuring that any defects are immediately identified and addressed.
This technology is a game-changer for the textile industry. By automating the inspection process, Svegea of Sweden not only improves accuracy but also frees up human inspectors to focus on more complex tasks that require a human touch. This blend of AI and human expertise creates a more efficient and effective inspection process.
Benefits of AI in Fabric Inspection
The benefits of using AI for fabric inspection are manifold. Firstly, it enhances accuracy. AI systems can detect even the smallest defects, ensuring that only the best fabrics make it to the market. This level of precision is difficult to achieve with manual inspection alone.
Secondly, AI-driven inspection systems are incredibly efficient. They can process large volumes of fabric quickly, reducing the time required for inspection and speeding up the overall production process. This efficiency translates into cost savings for manufacturers, as they can produce more in less time.
Moreover, AI systems are consistent. Unlike human inspectors, who may have varying levels of attention and expertise, AI systems provide uniform quality control. This consistency is crucial for maintaining high standards across all products.
Real-World Applications
The real-world applications of AI in fabric inspection are impressive. For example, companies using AI technology have reported significant reductions in defect rates and improvements in overall product quality. This technology is not just a theoretical concept; it is being used successfully in the industry today.
Svegea of Sweden’s AI-powered fabric inspection machines is a testament to this success. By leveraging AI, they have been able to enhance their inspection processes, ensuring that their fabrics meet the highest quality standards. This commitment to quality has helped them build a strong reputation in the industry.
The Future of Fabric Inspection
Looking ahead, the future of fabric inspection lies in further advancements in AI technology. As AI systems become more sophisticated, they will be able to detect even more subtle defects and provide even greater accuracy. This will set new benchmarks for quality control in the textile industry.
Additionally, the integration of AI with other technologies, such as the Internet of Things (IoT) and machine learning, will open up new possibilities for fabric inspection. For instance, IoT-enabled sensors can provide real-time data on fabric conditions, which AI systems can analyze to predict potential defects before they occur.
Revolutionizing the Fabric Inspection Technology
AI technology is revolutionizing fabric inspection, making it more accurate, efficient, and consistent. Companies like Svegea of Sweden are leading the way, demonstrating the immense potential of AI in the textile industry. By embracing this technology, manufacturers can ensure that their fabrics meet the highest quality standards, enhancing their reputation and customer satisfaction.
If you are interested in learning more about how AI can transform your fabric inspection processes, visit Svegea of Sweden’s fabric inspection page. Discover how their innovative solutions can help you achieve unparalleled quality control in your textile production.
Choosing the right textile machinery can be a daunting task, especially with the plethora of options available in the market. The decision impacts your production efficiency, product quality, and overall business profitability. Here are some key tips to help you navigate this critical process.
1. Understand Your Production Needs
Before investing in textile machinery, it’s crucial to understand your specific production needs. Different types of machinery serve various purposes, from weaving and knitting to dyeing and finishing. Determine the scale of your operations, the types of textiles you produce, and your production goals. This understanding will guide your choice of machinery that best suits your requirements.
2. Evaluate Technology and Features
Modern textile machinery comes with a range of advanced technologies and features designed to enhance productivity and quality. Look for machines that offer automation, precision control, and energy efficiency. For instance, Svegea of Sweden offers cutting-edge machinery equipped with the latest technology, ensuring high efficiency and minimal waste. Our products are known for their durability and innovative features.
3. Consider Quality and Reliability
Quality and reliability are paramount when choosing textile machinery. Investing in high-quality machines may come with a higher initial cost, but it ensures long-term performance and fewer breakdowns. Research and compare different brands, read reviews, and consider the manufacturer’s reputation. Modesty aside, our brand has a proven track record of producing reliable and high-quality textile machinery.
4. Assess After-Sales Support and Maintenance
After-sales support and maintenance services are crucial for the smooth operation of textile machinery. Ensure that the manufacturer offers comprehensive support, including installation, training, and regular maintenance services. We provide excellent customer support and maintenance services, ensuring that your machinery operates optimally.
5. Analyze Cost and Return on Investment (ROI)
While the cost of textile machinery is a significant factor, it’s essential to consider the return on investment (ROI). A more expensive machine with advanced features and higher efficiency can lead to cost savings in the long run. Calculate the total cost of ownership, including maintenance and operational costs, and compare it with the expected benefits. Opt for machines that offer the best value for money.
6. Environmental Considerations
Sustainability is a growing concern in the textile industry. Choose machinery that is energy-efficient and environmentally friendly. Machines that reduce water and chemical usage, minimize waste, and consume less energy are ideal. This Swedish textile company is known for producing sustainable textile machinery that aligns with eco-friendly production practices.
7. Compatibility with Existing Systems
Ensure that the new machinery is compatible with your existing systems and processes. Incompatibility can lead to production delays and additional costs. Consult with the manufacturer or a technical expert to evaluate the integration process. A company that offers flexible machinery solutions that can be seamlessly integrated into various production setups, should be the right choice.
Explore Svegea of Sweden’s Textile Machinery
Choosing the right textile machinery is a critical decision that impacts your production efficiency and product quality. By considering factors such as your production needs, technology and features, quality, after-sales support, cost, environmental impact, and compatibility, you can make an informed choice. Svegea of Sweden’s innovative machinery solutions are designed to meet diverse production requirements while ensuring high efficiency and sustainability.
Curious about how we can elevate your textile production process? Visit our product page for more information and start your journey towards optimal textile production today.
In the quest for sustainable fashion, choosing the right fabrics is crucial. Eco-friendly fabric choices not only reduce environmental impact but also promote ethical production practices. This guide explores some of the best sustainable fabrics and their benefits.
Understanding Eco-Friendly Fabrics
Eco-friendly fabrics are made from natural, renewable, or recycled materials that have a lower environmental footprint compared to conventional fabrics. These fabrics are produced using methods that minimize water usage, chemical treatments, and energy consumption.
Popular Eco-Friendly Fabrics
- Organic Cotton: Grown without harmful pesticides and synthetic fertilizers, organic cotton is a popular choice for sustainable fashion. It is soft, breathable, and biodegradable.
- Bamboo: Bamboo fabric is made from the pulp of bamboo grass, which grows quickly and requires minimal water and pesticides. It is naturally antibacterial and moisture-wicking.
- Hemp: Hemp is a highly sustainable crop that requires little water and no pesticides. It produces a durable and versatile fabric that is perfect for various types of clothing.
- Recycled Polyester: Made from recycled plastic bottles, recycled polyester reduces waste and conserves resources. It is often used in activewear due to its durability and moisture-wicking properties.
- Tencel (Lyocell): Tencel is a sustainable fabric made from wood pulp sourced from responsibly managed forests. It is biodegradable, soft, and has a silky feel.
The Environmental Impact
Choosing eco-friendly fabrics significantly reduces the environmental impact of fashion production. These fabrics require fewer resources, produce less waste, and are often biodegradable or recyclable. By opting for sustainable fabrics, designers and consumers can contribute to a greener planet.
Economic Benefits
Sustainable fabrics are not only good for the environment but also for business. As consumers become more environmentally conscious, there is a growing demand for eco-friendly products. Brands that use sustainable fabrics can attract a loyal customer base willing to pay a premium for ethical and eco-friendly fashion.
Challenges and Innovations
While eco-friendly fabrics offer many benefits, there are challenges in their production and adoption. The cost of sustainable materials can be higher, and the supply chain may be less established compared to conventional fabrics. However, innovations in textile technology and increased consumer awareness are helping to overcome these challenges.
Success Stories
Many brands are leading the way in sustainable fashion by using eco-friendly fabrics. For example, Patagonia uses recycled polyester in its clothing, and Stella McCartney incorporates organic cotton and Tencel in her designs. These brands demonstrate that sustainability and style can coexist.
The Future of Fashion
The future of fashion lies in sustainability. By choosing eco-friendly fabrics, the industry can reduce its environmental footprint and create a more ethical production process. As more brands and consumers embrace sustainable practices, we can look forward to a fashion industry that is both stylish and environmentally responsible.
Cutting Edge Technology
Svegea of Sweden provides cutting-edge technology that complements the zero waste cutting process, enabling manufacturers to take their sustainability initiatives to the next level. With the Euro Collarette Cutter, Svegea offers a solution that not only minimizes fabric waste but also boosts production efficiency and cost-effectiveness. Euro Collarette Cutters are designed to optimize fabric cutting processes, providing highly efficient solutions that align with zero waste cutting principles. These machines are integral for manufacturers aiming to reduce fabric waste, streamline production, and meet sustainability goals.
Key Features of Svegea’s Euro Collarette Cutters:
- Precision Cutting: Euro Collarette Cutters are renowned for their precise, consistent cutting ability, reducing the amount of fabric waste that typically results from inefficient manual cutting techniques.
- Flexibility in Fabric Handling: These machines are capable of handling various fabric types and thicknesses, making them versatile for different garment production needs. This flexibility ensures minimal waste regardless of the fabric used, supporting zero waste pattern cutting.
- Automation and Efficiency: The advanced automation technology integrated into Svegea’s cutters allows for higher production speeds while maintaining precision. Automation reduces the likelihood of human error, further minimizing material waste.
- Sustainability-Driven Design: Svegea develops its cutting machines with a strong focus on sustainability, ensuring that they minimize fabric waste to nearly zero. These solutions seamlessly integrate into eco-conscious production environments, allowing manufacturers to adopt greener practices while enhancing efficiency.
- Cost Savings: By maximizing fabric use, these machines reduce raw material costs, contributing to both economic and environmental benefits for manufacturers adopting zero waste practices.
Contact us to explore how Svegea’s Euro Collarette Cutters can transform your production line for a more sustainable future.
In the dynamic world of textile manufacturing, automation is a cornerstone of innovation, driving unprecedented efficiency, precision, and sustainability. As an expert with over two decades of experience in textile automation, we have witnessed firsthand the transformative power of these technologies. Today, we’ll explore how automation is reshaping the fabric of our industry.
The Evolution of Textile Automation
The journey from hand-spun fibers to today’s high-tech production lines tells a story of relentless innovation. Early mechanization during the Industrial Revolution laid the groundwork, but modern automation has catapulted us into a new era of manufacturing excellence.
Key milestones include:
1. 1960s-1970s: Introduction of computer-controlled looms
2. 1980s-1990s: Development of robotic systems for material handling
3. 2000s-2010s: Integration of AI and machine learning in quality control
4. 2020s and beyond: Emergence of fully automated, smart textile factories
Core Areas Transformed by Automation
Spinning: Precision at Lightning Speeds
Modern spinning systems, such as rotor and air-jet technologies, have revolutionized yarn production. These systems can produce yarn up to 20 times faster than traditional ring spinning, with unparalleled consistency.
Weaving: Intelligent Looms for Flawless Fabrics
Today’s computerized looms are marvels of engineering. There are machines for example that use real-time adaptive tension control to adjust warp tension on the fly, ensuring fabric quality remains consistent even as conditions change during production. This level of precision was unthinkable just a decade ago.
Dyeing and Finishing: Sustainability Meets Efficiency
Automated dyeing and finishing processes have dramatically reduced water and energy consumption while improving color consistency. Digital textile printing, exemplified by machines can print complex designs directly onto fabric at up to 1,000 m²/hour, revolutionizing small-batch and customized production.
Spotlight on Innovation: Svegea’s EC 450 XF Collarette Cutting System
The EC 450 XF Collarette Cutting System by Svegea represents the cutting edge of textile automation. As the winner of the Texprocess Americas 2023 Innovation Award, this system exemplifies how targeted automation can solve specific industry challenges.
Key features include:
– Multi-material compatibility for unparalleled versatility
– Precision cutting with minimal waste
– Rapid changeover times, boosting overall productivity
The EC 450 XF doesn’t just cut fabric; it redefines efficiency in garment manufacturing. For manufacturers looking to stay competitive, systems like this are not just beneficial—they’re essential.
The Tangible Benefits of Automation
1. Quality Assurance: Automated systems consistently produce high-quality textiles, reducing defects by up to 90% compared to manual processes.
2. Increased Productivity: Modern automated lines can operate 24/7, increasing output by 200-300% over traditional methods.
3. Cost Reduction: While initial investment is significant, automated systems can reduce labor costs by 40-60% and material waste by 20-30% over their lifetime.
4. Customization at Scale: Automation enables quick changeovers, making small-batch and customized production economically viable.
5. Enhanced Safety: Automation minimizes human exposure to hazardous processes, reducing workplace accidents by up to 80% in some facilities.
Overcoming Implementation Challenges
While the benefits of automation are clear, implementation comes with challenges:
1. Initial Investment: The upfront cost of automation can be substantial. However, ROI typically occurs within 2-5 years, depending on the scale of implementation.
2. Workforce Transition: Shifting to automated systems requires retraining staff. Forward-thinking companies are investing in upskilling programs to transition workers into higher-value roles.
3. System Integration: Ensuring new automated systems work seamlessly with existing processes is crucial. Careful planning and phased implementation can mitigate disruptions.
The Future of Textile Automation
Looking ahead, several trends will shape the future of textile automation:
1. AI and Machine Learning: These technologies will enable predictive maintenance and real-time quality control, further improving efficiency and reducing downtime.
2. Internet of Things (IoT): Connected devices will create smart factories where every aspect of production is monitored and optimized in real-time.
3. Sustainable Automation: Future systems will focus even more on reducing environmental impact, with closed-loop water systems and energy-efficient processes.
4. Collaborative Robotics: Cobots will work alongside humans, handling repetitive tasks while allowing human workers to focus on high-value activities.
Embracing the Automated Future
Automation in textile manufacturing isn’t just about replacing human labor—it’s about augmenting human capabilities, driving innovation, and creating a more sustainable, efficient industry. As we look to the future, it’s clear that automation will play an increasingly central role in shaping the textiles of tomorrow.
For manufacturers, the message is clear: embrace automation or risk being left behind. The future of textiles is automated, and that future is now.
To explore cutting-edge automation solutions like Svegea’s EC 450 XF Collarette Cutting System, contact us now! For those ready to take the next step in their automation journey, now is the time to act.
The textile manufacturing industry is undergoing a significant transformation. As we move into 2025, several trends are shaping the future of this dynamic sector. From sustainable practices to advanced technologies, the landscape is evolving rapidly. Let’s explore the top trends in textile manufacturing for 2024 and 2025.
1. Sustainable Practices
Sustainability is no longer a buzzword; it’s a necessity. Textile manufacturers are increasingly adopting eco-friendly practices to reduce their environmental footprint. This includes using organic materials, recycling waste, and implementing energy-efficient processes. According to the World Economic Forum, sustainable practices in textile manufacturing can significantly reduce carbon emissions and water usage.
2. Advanced Technologies
The integration of advanced technologies is revolutionizing textile manufacturing. Automation, artificial intelligence (AI), and the Internet of Things (IoT) are enhancing efficiency and productivity. For instance, AI-driven machines can predict maintenance needs, reducing downtime and increasing output. The International Textile Manufacturers Federation highlights that these technologies are crucial for staying competitive in the global market.
3. Customization and Personalization
Consumers today demand unique and personalized products. Textile manufacturers are leveraging digital printing and other technologies to offer customized solutions. This trend is particularly evident in the fashion industry, where personalized clothing is gaining popularity. A report by McKinsey & Company suggests that customization will be a key driver of growth in the textile sector.
4. Smart Textiles
Smart textiles, also known as e-textiles, are gaining traction. These textiles have embedded sensors and electronics that can monitor health, track fitness, and even change color. The potential applications are vast, ranging from healthcare to sportswear. According to TechCrunch, the smart textiles market is expected to grow exponentially in the coming years.
5. Ethical Labor Practices
Consumers are becoming more conscious of the ethical implications of their purchases. As a result, textile manufacturers are focusing on fair labor practices and ensuring safe working conditions. This shift is not only ethical but also beneficial for brand reputation. The Fair Labor Association provides guidelines and resources for companies aiming to improve their labor practices.
Spotlight on Svegea of Sweden
Svegea of Sweden is a notable player in the textile manufacturing industry. Known for their innovative solutions, Svegea offers advanced slitting and cutting machines that enhance efficiency and precision. Their commitment to quality and sustainability sets them apart in the market. While not overtly promotional, it’s worth noting how companies like Svegea are contributing to the industry’s evolution.
Exciting Changes
The textile manufacturing industry is poised for exciting changes in 2025. From sustainable practices to advanced technologies, the trends shaping this sector are both innovative and impactful. By staying informed and adapting to these trends, manufacturers can thrive in a competitive landscape.
For innovative and sustainable textile machinery, contact Svegea of Sweden. Our advanced solutions can help you stay ahead in the evolving textile industry.
The textile industry has always been a pioneer in technological advancements. From the spinning jenny to modern automated looms, the sector has continually evolved. Today, the integration of Artificial Intelligence (AI) into textile machines marks the latest leap forward, offering unparalleled efficiency, precision, and productivity. This article delves into how AI textile machines are revolutionizing the industry and highlights a cutting-edge product from Svegea of Sweden.
The Rise of AI in Textile Manufacturing
AI is no longer a futuristic concept; it is now a vital component of the manufacturing sector, especially in textiles. The industry is swiftly adopting AI technologies to enhance production processes, improve product quality, and reduce waste. AI-powered machines can analyze vast amounts of data in real time, enabling more informed decision-making and streamlined operations.
AI’s ability to learn from data and make real-time adjustments has transformed textile manufacturing. These machines can predict when a process needs adjustment, reducing downtime and boosting overall efficiency. For instance, AI can optimize machine settings based on the fabric type, ensuring each material is handled with utmost care and precision.
Reducing Waste and Enhancing Sustainability
One of the most significant benefits of AI-integrated textile machines is their ability to minimize waste. Traditional manufacturing often results in excess material being discarded, increasing costs and environmental impact. AI can significantly reduce this waste by optimizing cutting and sewing processes.
AI algorithms can analyze fabric patterns to determine the most efficient cutting method, minimizing leftover scraps. This not only reduces waste but also lowers costs for manufacturers. Additionally, AI can monitor fabric quality throughout production, identifying and correcting defects early.
Reducing waste also supports the industry’s sustainability efforts. As demand for eco-friendly products grows, manufacturers face increasing pressure to adopt sustainable practices. AI textile machines play a crucial role in this shift by enabling more efficient resource use and reducing the carbon footprint of textile production.
Enhancing Productivity with AI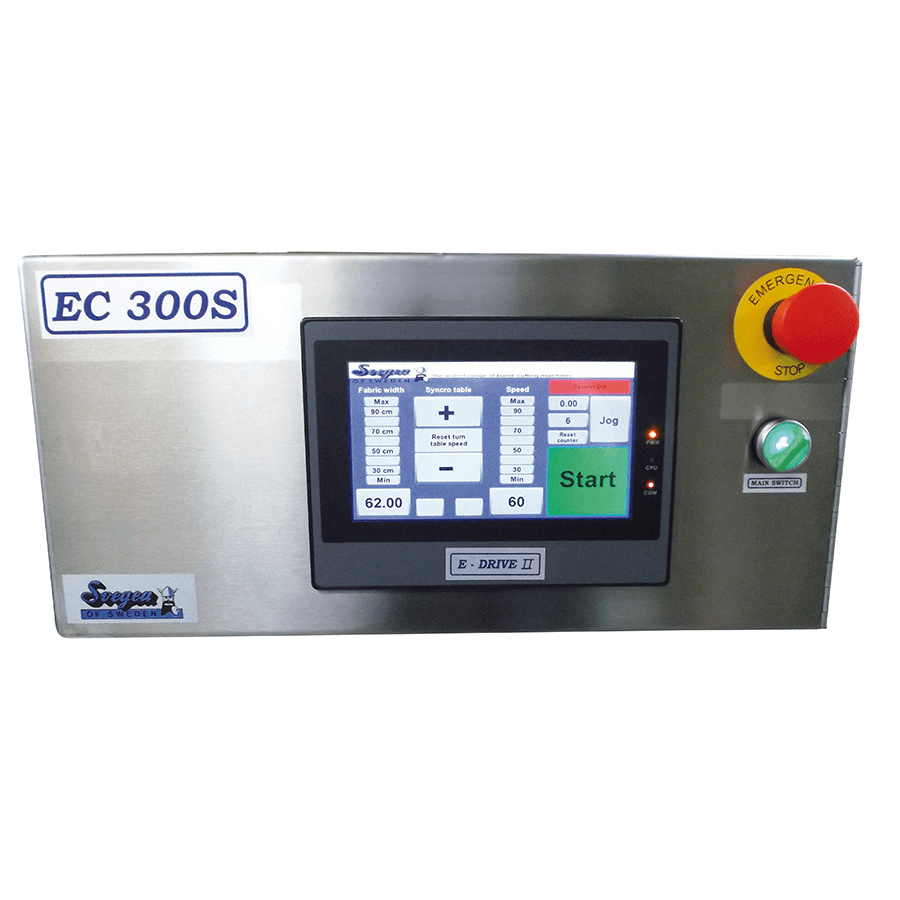
Productivity is a key metric in any manufacturing environment, and the textile industry is no exception. AI-integrated machines are designed to maximize output without compromising quality. By automating routine tasks, these machines free up human workers to focus on more complex, value-added activities.
For example, AI can automate the inspection process, quickly identifying defects that human inspectors might miss. This speeds up the production line and ensures only the highest-quality products reach the market. Additionally, AI can predict machine failures, allowing for preventative maintenance that minimizes downtime.
AI also excels in predictive analytics. By analyzing historical data, AI can forecast demand for specific products, enabling manufacturers to adjust production schedules accordingly. This ensures they can meet customer demand without overproducing, further reducing waste and costs.
Spotlight on Svegea’s AI-Integrated Textile Machines
Svegea of Sweden is a leading innovator in the textile machinery industry, known for its commitment to quality and efficiency. One standout product is the EC 300 Collarette Cutter, an AI-integrated machine that exemplifies the benefits of modern technology in textile manufacturing.
The EC 300 optimizes the cutting process, ensuring precision and consistency with every cut. With AI at its core, the machine can analyze fabric and make real-time adjustments to cutting parameters, reducing waste and enhancing efficiency. The result is a product that meets and exceeds the high standards expected by today’s manufacturers.
Svegea’s commitment to innovation extends beyond this. The company continuously invests in research and development, ensuring its machines remain at the cutting edge of technology. By integrating AI into its products, Svegea leads the charge toward a more efficient, sustainable, and productive textile industry.
To learn more about Svegea’s AI-integrated textile machines, talk to us now!
In today’s fast-paced world, consumers are increasingly seeking unique and personalized fashion experiences. This shift is reshaping the fashion industry, pushing brands to innovate and offer more customized products and services. One key player in this transformation is Svegea, whose Fabric Inspection tools are making a significant impact.
The Demand for Personalization
Personalized fashion experiences are no longer a luxury but a necessity for many consumers. According to recent studies, a significant majority of shoppers prefer brands that offer personalized options. This trend is driven by the desire for individuality and the need to stand out in a crowded market. Personalized fashion experiences allow consumers to express their unique style and preferences, creating a deeper connection with the brand.
How Technology is Enabling Customization
Advancements in technology have made it easier for fashion brands to offer personalized experiences. From AI-powered virtual fitting rooms to customized recommendations based on browsing history, technology is at the forefront of this revolution. Svegea’s Fabric Inspection tools play a crucial role in this process by ensuring the quality and precision of customized garments.
The Benefits of Fabric Inspection
Fabric inspection is a critical step in the production of personalized garments. It ensures that each piece meets the quality standards expected by consumers. Svegea’s Fabric Inspection tools are designed to detect even the smallest imperfections, allowing brands to address issues before they reach the customer. This not only enhances the overall quality of the product but also builds trust and loyalty among consumers.
Customization Beyond Fabric Inspection
While fabric inspection is vital, Svegea’s capabilities extend beyond this. The company can customize its machines to fit the specific production needs of its clients. This flexibility allows fashion brands to optimize their production processes and offer truly unique products. Whether it’s adjusting the machine settings for different fabric types or integrating new technologies, Svegea’s customized solutions ensure that brands can meet the growing demand for personalized fashion experiences.
The Future of Personalized Fashion
The trend towards personalized fashion experiences shows no signs of slowing down. As consumers continue to seek unique and customized products, brands must adapt to stay competitive. Svegea’s innovative solutions, including its Fabric Inspection tools, will play a crucial role in this evolution. By ensuring quality and enabling customization, Svegea is helping to shape the future of the fashion industry.
Transforming the Industry
Personalized fashion experiences are transforming the industry, driven by consumer demand for uniqueness and individuality. Technology, including Svegea’s Fabric Inspection tools, is enabling this shift by ensuring quality and precision in customized garments. As the trend towards personalization continues to grow, Svegea’s innovative solutions will remain at the forefront, helping brands meet the evolving needs of their customers.
In an era where sustainability is paramount, the circular economy offers a transformative approach to how we produce and consume goods. Central to this concept are closed-loop systems and circular design, both of which aim to minimize waste and make the most of our resources.
Understanding Closed-Loop Systems
Closed-loop systems are designed to create a continuous cycle of use and reuse, effectively reducing waste. In these systems, the output of one process becomes the input for another, ensuring that materials are constantly recycled and repurposed. This approach not only conserves resources but also significantly reduces environmental impact.
The Importance of Circular Design
The circular design is a key element of the circular economy. It involves designing products with their entire lifecycle in mind, from creation to disposal. Circular design focuses on durability, reparability, and recyclability, making products easy to disassemble and reuse. This process reduces the need for new raw materials and minimizes waste.
Strategies for Minimizing Waste
Minimizing waste is a fundamental goal of the circular economy. This process is achievable through various strategies, including:
- Design for Longevity: Creating products that last longer and are easily repairable.
- Material Innovation: Using materials that are easier to recycle and have a lower environmental impact.
- Efficient Manufacturing: Implementing processes that reduce waste and improve resource efficiency.
Real-World Applications
Many companies are now adopting circular principles to enhance sustainability. For instance, in the textile industry, some manufacturers are focusing on producing high-quality trim that aligns with circular design principles. By ensuring that their products are durable and recyclable, these companies contribute to a more sustainable future.
The Benefits of a Circular Economy
The shift towards a circular economy offers numerous benefits:
- Environmental Sustainability: By reducing waste and conserving resources, the circular economy helps protect the environment.
- Economic Efficiency: Reusing materials and improving efficiency can lead to cost savings for businesses.
- Innovation and Growth: The circular economy encourages innovation, leading to new business opportunities and economic growth.
Representing a Significant Shift
The circular economy represents a significant shift in how we think about production and consumption. By embracing closed-loop systems and circular design, we can minimize waste and make better use of our resources. This approach not only benefits the environment but also offers economic advantages.
Sustainable Textile Manufacturing
Svegea of Sweden is leading the way in sustainable textile manufacturing with their EC 450 XF Collarette Cutting System. This innovative machine exemplifies circular economy principles by ensuring precision cutting, which minimizes material waste. Its versatility allows it to handle various fabrics and applications, making it an essential tool for manufacturers committed to sustainability. The EC 450 XF boosts energy efficiency, cuts power consumption, and aligns with global sustainability goals. By integrating such advanced technology, Svegea is making significant strides toward a more sustainable future in the textile industry.
To learn more about how quality trim can align with circular principles, visit Svegea’s contact page and discover their commitment to sustainability.