Ever wondered how fabrics impact your mood? The textures of the textiles we surround ourselves with can significantly influence our emotions and behavior. This article delves into the fascinating psychology of fabric textures and how they can shape our daily experiences.
The Power of Fabric Textures
Fabric texture refers to the surface quality of a fabric, which can be smooth, rough, soft, or stiff. Different textures evoke different emotional responses.
Smooth Textures: Fabrics like silk, satin, and cotton have smooth textures. These materials are often associated with luxury and comfort. Wearing smooth fabrics can make you feel more relaxed, elegant, and confident. They’re perfect for special occasions or when you want to pamper yourself.
Rough Textures: Fabrics like wool and raw silk are examples of rough textures. These materials can evoke feelings of ruggedness, durability, and strength. Wearing rough-textured fabrics can make you feel more grounded and resilient. They’re great for casual, everyday wear or outdoor activities.
Soft Textures: Fabrics such as velvet are incredibly soft. These fabrics are associated with warmth, comfort, and nurturing. Wearing soft, textured fabrics can make you feel cozy and secure, making them ideal for relaxing at home or during the colder months.
Stiff Textures: Fabrics like organza have a stiff texture. These fabrics often convey formality and structure. Wearing stiff fabrics can make you feel more disciplined and poised. They’re suitable for formal events or professional settings.
The Influence of Fabric Colors
Colors are powerful psychological tools that can influence our emotions and perceptions. Different colors can have varying effects on our mood.
Red: Red is a bold and stimulating color. It is often associated with passion, energy, and excitement. Wearing red can make you feel more confident and assertive. It’s a great choice for events where you want to stand out and make a strong impression.
Blue: Blue is a calming and soothing color, often linked to feelings of tranquility, trust, and stability. Wearing blue can help you feel more relaxed and at peace. It’s ideal for situations where you need to stay calm and composed, such as job interviews or exams.
Yellow: Yellow is a bright and cheerful color. It is associated with happiness, optimism, and creativity. Wearing yellow can lift your spirits and make you feel more joyful and energetic. It’s perfect for social gatherings or creative endeavors.
Green: Green is a refreshing and harmonious color. It represents nature, balance, and growth. Wearing green can make you feel more refreshed and rejuvenated.
Combining Textures and Colors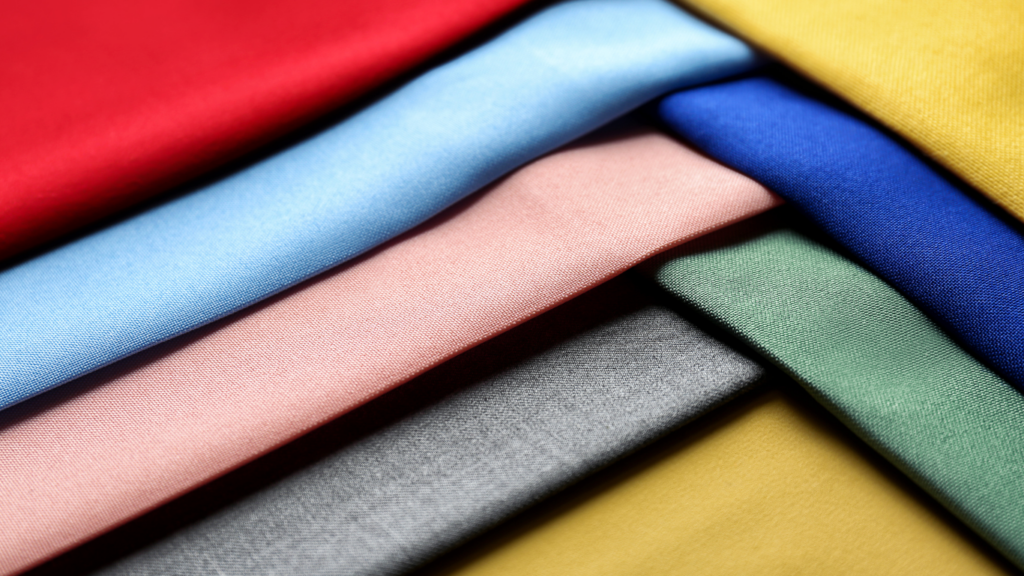
The combination of textures and colors can create a powerful impact on your mood and behavior. For instance, a smooth, blue silk dress can make you feel both elegant and calm, while a rough, red wool sweater can evoke feelings of strength and confidence. Understanding how these elements work together can help you make more informed choices about your wardrobe and home decor.
Svegea of Sweden: Innovating Textile Machinery
Svegea of Sweden is at the forefront of textile machinery innovation. Their advanced fabric-cutting machines ensure precision and efficiency, making it easier for designers to create garments that not only look good but also feel good. By investing in high-quality machinery from Svegea, manufacturers can produce textiles that meet the psychological needs of their customers.
Svegea leads the textile industry with its quality and innovation. Their machines cut various fabrics with utmost precision. This attention to detail helps create garments that provide the desired emotional and psychological benefits to the wearer.
A Fascinating Field
The psychology of fabric is a fascinating field that highlights the significant impact that textures and colors can have on our moods and behavior. By understanding these effects, we can make more informed choices about the fabrics we wear and surround ourselves with. Whether you’re looking to feel more confident, relaxed, or joyful, the right fabric can make all the difference.
For manufacturers and designers, investing in high-quality textile machinery from Svegea of Sweden can help ensure that your products meet the psychological needs of your customers. To learn more about Svegea’s innovative solutions, visit their contact page.
Explore the world of fabrics and discover how the textures and colors you choose can transform your mood and behavior. Make informed choices and experience the psychological benefits of the right textiles today!
In the dynamic world of textile manufacturing, automation is a cornerstone of innovation, driving unprecedented efficiency, precision, and sustainability. As an expert with over two decades of experience in textile automation, we have witnessed firsthand the transformative power of these technologies. Today, we’ll explore how automation is reshaping the fabric of our industry.
The Evolution of Textile Automation
The journey from hand-spun fibers to today’s high-tech production lines tells a story of relentless innovation. Early mechanization during the Industrial Revolution laid the groundwork, but modern automation has catapulted us into a new era of manufacturing excellence.
Key milestones include:
1. 1960s-1970s: Introduction of computer-controlled looms
2. 1980s-1990s: Development of robotic systems for material handling
3. 2000s-2010s: Integration of AI and machine learning in quality control
4. 2020s and beyond: Emergence of fully automated, smart textile factories
Core Areas Transformed by Automation
Spinning: Precision at Lightning Speeds
Modern spinning systems, such as rotor and air-jet technologies, have revolutionized yarn production. These systems can produce yarn up to 20 times faster than traditional ring spinning, with unparalleled consistency.
Weaving: Intelligent Looms for Flawless Fabrics
Today’s computerized looms are marvels of engineering. There are machines for example that use real-time adaptive tension control to adjust warp tension on the fly, ensuring fabric quality remains consistent even as conditions change during production. This level of precision was unthinkable just a decade ago.
Dyeing and Finishing: Sustainability Meets Efficiency
Automated dyeing and finishing processes have dramatically reduced water and energy consumption while improving color consistency. Digital textile printing, exemplified by machines can print complex designs directly onto fabric at up to 1,000 m²/hour, revolutionizing small-batch and customized production.
Spotlight on Innovation: Svegea’s EC 450 XF Collarette Cutting System
The EC 450 XF Collarette Cutting System by Svegea represents the cutting edge of textile automation. As the winner of the Texprocess Americas 2023 Innovation Award, this system exemplifies how targeted automation can solve specific industry challenges.
Key features include:
– Multi-material compatibility for unparalleled versatility
– Precision cutting with minimal waste
– Rapid changeover times, boosting overall productivity
The EC 450 XF doesn’t just cut fabric; it redefines efficiency in garment manufacturing. For manufacturers looking to stay competitive, systems like this are not just beneficial—they’re essential.
The Tangible Benefits of Automation
1. Quality Assurance: Automated systems consistently produce high-quality textiles, reducing defects by up to 90% compared to manual processes.
2. Increased Productivity: Modern automated lines can operate 24/7, increasing output by 200-300% over traditional methods.
3. Cost Reduction: While initial investment is significant, automated systems can reduce labor costs by 40-60% and material waste by 20-30% over their lifetime.
4. Customization at Scale: Automation enables quick changeovers, making small-batch and customized production economically viable.
5. Enhanced Safety: Automation minimizes human exposure to hazardous processes, reducing workplace accidents by up to 80% in some facilities.
Overcoming Implementation Challenges
While the benefits of automation are clear, implementation comes with challenges:
1. Initial Investment: The upfront cost of automation can be substantial. However, ROI typically occurs within 2-5 years, depending on the scale of implementation.
2. Workforce Transition: Shifting to automated systems requires retraining staff. Forward-thinking companies are investing in upskilling programs to transition workers into higher-value roles.
3. System Integration: Ensuring new automated systems work seamlessly with existing processes is crucial. Careful planning and phased implementation can mitigate disruptions.
The Future of Textile Automation
Looking ahead, several trends will shape the future of textile automation:
1. AI and Machine Learning: These technologies will enable predictive maintenance and real-time quality control, further improving efficiency and reducing downtime.
2. Internet of Things (IoT): Connected devices will create smart factories where every aspect of production is monitored and optimized in real-time.
3. Sustainable Automation: Future systems will focus even more on reducing environmental impact, with closed-loop water systems and energy-efficient processes.
4. Collaborative Robotics: Cobots will work alongside humans, handling repetitive tasks while allowing human workers to focus on high-value activities.
Embracing the Automated Future
Automation in textile manufacturing isn’t just about replacing human labor—it’s about augmenting human capabilities, driving innovation, and creating a more sustainable, efficient industry. As we look to the future, it’s clear that automation will play an increasingly central role in shaping the textiles of tomorrow.
For manufacturers, the message is clear: embrace automation or risk being left behind. The future of textiles is automated, and that future is now.
To explore cutting-edge automation solutions like Svegea’s EC 450 XF Collarette Cutting System, contact us now! For those ready to take the next step in their automation journey, now is the time to act.
The textile manufacturing industry is undergoing a significant transformation. As we move into 2025, several trends are shaping the future of this dynamic sector. From sustainable practices to advanced technologies, the landscape is evolving rapidly. Let’s explore the top trends in textile manufacturing for 2024 and 2025.
1. Sustainable Practices
Sustainability is no longer a buzzword; it’s a necessity. Textile manufacturers are increasingly adopting eco-friendly practices to reduce their environmental footprint. This includes using organic materials, recycling waste, and implementing energy-efficient processes. According to the World Economic Forum, sustainable practices in textile manufacturing can significantly reduce carbon emissions and water usage.
2. Advanced Technologies
The integration of advanced technologies is revolutionizing textile manufacturing. Automation, artificial intelligence (AI), and the Internet of Things (IoT) are enhancing efficiency and productivity. For instance, AI-driven machines can predict maintenance needs, reducing downtime and increasing output. The International Textile Manufacturers Federation highlights that these technologies are crucial for staying competitive in the global market.
3. Customization and Personalization
Consumers today demand unique and personalized products. Textile manufacturers are leveraging digital printing and other technologies to offer customized solutions. This trend is particularly evident in the fashion industry, where personalized clothing is gaining popularity. A report by McKinsey & Company suggests that customization will be a key driver of growth in the textile sector.
4. Smart Textiles
Smart textiles, also known as e-textiles, are gaining traction. These textiles have embedded sensors and electronics that can monitor health, track fitness, and even change color. The potential applications are vast, ranging from healthcare to sportswear. According to TechCrunch, the smart textiles market is expected to grow exponentially in the coming years.
5. Ethical Labor Practices
Consumers are becoming more conscious of the ethical implications of their purchases. As a result, textile manufacturers are focusing on fair labor practices and ensuring safe working conditions. This shift is not only ethical but also beneficial for brand reputation. The Fair Labor Association provides guidelines and resources for companies aiming to improve their labor practices.
Spotlight on Svegea of Sweden
Svegea of Sweden is a notable player in the textile manufacturing industry. Known for their innovative solutions, Svegea offers advanced slitting and cutting machines that enhance efficiency and precision. Their commitment to quality and sustainability sets them apart in the market. While not overtly promotional, it’s worth noting how companies like Svegea are contributing to the industry’s evolution.
Exciting Changes
The textile manufacturing industry is poised for exciting changes in 2025. From sustainable practices to advanced technologies, the trends shaping this sector are both innovative and impactful. By staying informed and adapting to these trends, manufacturers can thrive in a competitive landscape.
For innovative and sustainable textile machinery, contact Svegea of Sweden. Our advanced solutions can help you stay ahead in the evolving textile industry.
In an era where sustainability is paramount, the circular economy offers a transformative approach to how we produce and consume goods. Central to this concept are closed-loop systems and circular design, both of which aim to minimize waste and make the most of our resources.
Understanding Closed-Loop Systems
Closed-loop systems are designed to create a continuous cycle of use and reuse, effectively reducing waste. In these systems, the output of one process becomes the input for another, ensuring that materials are constantly recycled and repurposed. This approach not only conserves resources but also significantly reduces environmental impact.
The Importance of Circular Design
The circular design is a key element of the circular economy. It involves designing products with their entire lifecycle in mind, from creation to disposal. Circular design focuses on durability, reparability, and recyclability, making products easy to disassemble and reuse. This process reduces the need for new raw materials and minimizes waste.
Strategies for Minimizing Waste
Minimizing waste is a fundamental goal of the circular economy. This process is achievable through various strategies, including:
- Design for Longevity: Creating products that last longer and are easily repairable.
- Material Innovation: Using materials that are easier to recycle and have a lower environmental impact.
- Efficient Manufacturing: Implementing processes that reduce waste and improve resource efficiency.
Real-World Applications
Many companies are now adopting circular principles to enhance sustainability. For instance, in the textile industry, some manufacturers are focusing on producing high-quality trim that aligns with circular design principles. By ensuring that their products are durable and recyclable, these companies contribute to a more sustainable future.
The Benefits of a Circular Economy
The shift towards a circular economy offers numerous benefits:
- Environmental Sustainability: By reducing waste and conserving resources, the circular economy helps protect the environment.
- Economic Efficiency: Reusing materials and improving efficiency can lead to cost savings for businesses.
- Innovation and Growth: The circular economy encourages innovation, leading to new business opportunities and economic growth.
Representing a Significant Shift
The circular economy represents a significant shift in how we think about production and consumption. By embracing closed-loop systems and circular design, we can minimize waste and make better use of our resources. This approach not only benefits the environment but also offers economic advantages.
Sustainable Textile Manufacturing
Svegea of Sweden is leading the way in sustainable textile manufacturing with their EC 450 XF Collarette Cutting System. This innovative machine exemplifies circular economy principles by ensuring precision cutting, which minimizes material waste. Its versatility allows it to handle various fabrics and applications, making it an essential tool for manufacturers committed to sustainability. The EC 450 XF boosts energy efficiency, cuts power consumption, and aligns with global sustainability goals. By integrating such advanced technology, Svegea is making significant strides toward a more sustainable future in the textile industry.
To learn more about how quality trim can align with circular principles, visit Svegea’s contact page and discover their commitment to sustainability.
Smart textiles, also known as electronic or e-textiles, represent a groundbreaking fusion of fashion and technology. These textiles go beyond mere wearability; they are programmable, interactive, and functional. In this article, we’ll explore what smart fabrics are, provide real-life examples, and discuss their future implications.
What Are Smart Materials?
Also called intelligent or responsive materials, these types of fabrics automatically respond to external stimuli such as temperature changes, light, pressure, or electric fields. Unlike traditional materials with static properties, interactive materials can adapt and change their properties based on environmental conditions. For instance:
– Piezoelectric materials generate voltage when pressure is applied.
– Shape memory alloys return to their original form after deformation.
– Thermochromic materials change color with temperature variations.
Enter Smart Fabrics
A subset of smart materials, these special fabrics embed digital components directly into textiles. These fabrics can:
- Conduct electricity
- React to environmental changes
- Gather and transmit data
- Incorporate embedded LED lights
Examples of Intelligent Fabrics
1. Thermochromic Fabrics: These fabrics change color in response to temperature variations, finding applications in fashion and safety gear.
2. Conductive Fabrics: Embedded with conductive threads, these fabrics transmit electrical signals and are used in wearable electronics.
3. Self-Healing Fabrics: Developed with materials that repair themselves after being punctured or torn.
Cutting-Edge Innovations
Researchers at Cambridge University have woven a 46-inch textile display loaded with LEDs, sensors, and energy storage. This e-textile can display different images or colors based on input from fiber-based devices like light, touch, and temperature sensors. The textile’s multi-functionality and compatibility with existing industrial manufacturing processes make it truly unique.
Image Source: https://www.cam.ac.uk/research/news/scientists-develop-fully-woven-smart-display
Healthcare and Beyond
Responsive fabrics embedded with sensors could transform everyday clothing into interactive devices. Imagine garments that track health metrics or provide real-time environmental feedback.
Tech textiles are more than just fabrics; they’re a canvas for innovation, bridging the gap between style and functionality. As technology advances, we can expect even more exciting developments in this field.
Remember, the future of fashion isn’t just about what you wear—it’s about what your clothes can do for you!
Luxury has evolved beyond mere opulence and exclusivity. It now tells the story of each design piece, highlighting meticulous craftsmanship and a commitment to ethical and sustainable practices. This article explores the world of high-end textiles, with fabric production as its cornerstone.
The Artisans and Their Craft
At the heart of luxury textiles are talented artisans. These skilled craftsmen and women create exquisite fabrics with unparalleled attention to detail. Every stitch, cut, and curve reflects their dedication, driving the continuous evolution of luxury with highly sought-after designs.
Slow Design and Bespoke Quality
Artisanal textiles are deeply rooted in craftsmanship. Unlike mass-produced goods, these items are created meticulously and thoughtfully. This movement, known as Slow Design, celebrates quality over quantity. Each piece is a unique work of art, reflecting the artisan’s expertise and passion.
The Journey from Fiber to Fabric
1. Fiber Selection: Luxury textiles begin with carefully chosen raw materials. Whether it’s silk, cashmere, or organic cotton, the quality of the fiber sets the foundation for the final product.
2. Spinning and Weaving: Artisans spin the fibers into yarns, which are then woven into fabric. Jacquard looms, guided by intricate patterns, produce complex designs that grace haute couture and high-end interiors.
3. Dyeing and Finishing: Artisans meticulously curate the color palette and apply dyes precisely. Finishing techniques—such as mercerization or calendering—enhance texture and luster.
4. Hand Embellishments: Embroidery, beading, and appliqué add a touch of luxury. Skilled hands transform plain fabric into wearable art.
The Role of Svegea of Sweden
Svegea of Sweden, a renowned textile machinery manufacturer, plays a crucial role in luxury fabric production. Their cutting-edge machines enable precise weaving, intricate patterns, and flawless finishes. From jacquard looms to automated knitting devices, Svegea’s technology empowers artisans to create fabrics that define luxury.
Subscribe to our blog for more insights into the world of luxury textiles, craftsmanship, and sustainable practices. Stay informed and inspired as we unravel the secrets behind high-end fabrics.
In the ever-evolving textile industry, innovation, and sustainability are paramount. One company leading the charge in this space is Svegea of Sweden. Renowned for its state-of-the-art cutting machines, Svegea combines advanced technology with eco-friendly practices to revolutionize textile manufacturing.
The Rise of Eco-Friendly Cutting Machines
As the demand for sustainable solutions in the textile industry grows, Svegea has positioned itself at the forefront. The company’s cutting machines are designed with a strong emphasis on reducing environmental impact. These machines not only enhance efficiency but also minimize waste, setting a new standard for eco-friendly manufacturing.
Svegea’s cutting machines incorporate several features that make them stand out. Firstly, they use energy-efficient motors that consume less power, resulting in lower carbon emissions. Additionally, the precision of these machines ensures that fabric waste is significantly reduced. This is a major concern in traditional textile production methods.
Innovative Technology for a Greener Future
Svegea’s commitment to sustainability goes beyond just reducing waste. Their cutting machines are equipped with advanced technology that supports the use of recycled materials. This capability is crucial for textile manufacturers aiming to meet the increasing consumer demand for eco-friendly products.
One of the key technological advancements in Svegea’s machines is the integration of AI-driven precision cutting. This technology allows for optimal use of fabric, ensuring that every inch of material is utilized effectively. By maximizing fabric use, manufacturers can significantly cut down on waste, contributing to a greener future.
Efficiency Meets Sustainability
Efficiency and sustainability are often seen as two competing goals in manufacturing. However, Svegea has successfully merged these two objectives with their cutting machines. The company’s machines are designed to deliver high-speed cutting without compromising on quality or environmental standards.
Svegea’s machines also feature user-friendly interfaces that allow operators to quickly adapt to new cutting patterns and materials. This adaptability not only enhances productivity but also reduces downtime, leading to more efficient production cycles. By streamlining operations, manufacturers can achieve higher output while maintaining sustainable practices.
Reducing Environmental Impact
The textile industry has long been criticized for its environmental footprint. Traditional cutting methods often result in significant fabric waste, contributing to landfill overflows and environmental degradation. Svegea addresses this issue head-on with their cutting-edge machines.
Svegea engineers their cutting machines to minimize fabric waste using precise cutting technology. This precision not only reduces waste but also maintains the quality of the cut pieces. By producing more usable fabric pieces per roll, Svegea helps manufacturers reduce their material costs and environmental impact.
Commitment to Continuous Improvement
A sustainability-conscious company demonstrates its dedication to innovation through its continuous efforts to improve its cutting machines. The company invests heavily in research and development to stay ahead of industry trends and meet the evolving needs of textile manufacturers.
Svegea regularly updates its machines with the latest technological advancements. This commitment to continuous improvement ensures that their cutting machines remain at the forefront of the industry. They do so while providing manufacturers with the best possible tools for sustainable production.
Customer-Centric Approach
At the heart of Svegea’s success is its customer-centric approach. The company works closely with textile manufacturers to understand their specific needs and challenges. This collaboration enables Svegea to tailor their cutting machines to meet the unique requirements of their clients.
Svegea offers comprehensive support and training to help manufacturers get the most out of their cutting machines. This support extends beyond the initial purchase, with ongoing maintenance and updates to ensure the machines continue to operate at peak efficiency. By prioritizing customer satisfaction, Svegea has built a loyal client base that values its innovative and eco-friendly solutions.
Svegea of Sweden is a pioneer in the textile industry, setting new standards with their eco-friendly cutting machines. By combining advanced technology with sustainable practices, Svegea is helping manufacturers reduce waste, improve efficiency, and meet the growing demand for environmentally responsible products. Its commitment to continuous improvement and customer satisfaction ensures that Svegea will remain a leader in the industry for years to come.
In the fast-paced world of textile manufacturing, precision and efficiency are paramount. The Roll-to-Roll Slitting Machine RRS-800 is a cutting-edge solution that meets these demands, allowing textile producers to optimize their processes and deliver high-quality products. In this article, we’ll explore the key features of this machine, its specifications, and its impact on the industry.
Key Features:
Motorized Knife with Adjustable Speed
The heart of this efficient slitting machine lies in its motorized knife. This advanced feature allows operators to control the cutting speed, ensuring precise slitting without compromising quality. Whether it’s delicate fabrics or heavy-duty materials, the RRS-800 adapts effortlessly.
Adjustable Cutting Widths
Flexibility is essential in textile production. This state-of-the-art textile machine achieves this by allowing operators to adjust cutting widths. By moving the placement of the knives, manufacturers can tailor the machine to their specific needs.
Optional Electronic Meter Counter
Keeping track of material usage is crucial for cost management. It offers an optional electronic meter counter, enabling real-time monitoring. This feature ensures efficient resource allocation and minimizes waste.
Pneumatic Lift Kit for Easy Loading and Start-Up
Loading and starting up a slitting machine can be labor-intensive. The RRS-800 streamlines this process with its pneumatic lift kit. Operators can effortlessly raise the knife shaft, reducing downtime and enhancing productivity.
Re-Rolling Efficiency
After slitting, re-rolling becomes essential. This cost-effective machine excels in this aspect by utilizing two independent air-expanding shafts. These shafts handle the re-rolling of slit rolls, ensuring uniform tension and preventing material distortion.
Three Shafts for Optimal Performance
The RRS-800 boasts a total of three shafts:
- One for the master roll
- Two for re-rolling
This configuration allows seamless transitions between processes, minimizing downtime and maximizing throughput.
Customizable Air-Shaft Sizes
Different materials require different handling. This slitting machine caters to this diversity by offering customizable air-shaft sizes upon request. Garment manufacturers can fine-tune the machine to match their specific textile types and dimensions.
The RRS-800 combines innovation, precision, and adaptability, making it a valuable asset for textile manufacturers worldwide. As the industry continues to evolve, machines like the RRS-800 are pivotal in meeting production demands while maintaining product quality.
The dynamic world of textile design and manufacturing is driven by innovation, shaping the industry’s future. From embracing sustainable practices to integrating cutting-edge technology, there’s a profound evolution underway. This shift promises enhanced efficiency and a more environmentally conscious approach to production. It’s an exciting time where creativity meets sustainability in every thread of the textile industry.
Sustainability in Textile Design:
Consumers increasingly demand eco-friendly products, prompting manufacturers to adopt sustainable practices throughout production. Svegea of Sweden, a leader in sustainable textile machinery innovations, champions sustainability with its state-of-the-art equipment designed to reduce waste and energy consumption while maintaining high-quality standards.
Digitalization and Efficiency:
The integration of digital technologies such as Artificial Intelligence (AI) and the Internet of Things (IoT) has revolutionized manufacturing processes. Svegea’s advanced machines leverage AI algorithms to optimize production efficiency, ensuring precise cuts and minimizing material wastage.
Customization for Consumer Preferences:
Customization is key as consumers increasingly desire unique and personalized products. Manufacturers are responding by offering customizable solutions tailored to consumer preferences. Svegea of Sweden collaborates with industry leaders to deliver intricate designs and patterns, meeting the growing demand for personalized textiles.
Collaborative Innovation:
Industry players are forging strategic partnerships to leverage collective expertise and resources. Svegea’s collaboration with textile industry leaders fosters innovation and knowledge exchange, driving continuous improvement in design and manufacturing processes.
Automation for Productivity:
Automated systems streamline production, reduce manual labor, and improve overall efficiency. The latest automated textile machines incorporate advanced robotics and AI, ensuring consistent quality across production batches.
Smart Textiles and Future Possibilities:
The adoption of smart textiles embedded with sensors and actuators is revolutionizing wearable technology. Innovative machines play a crucial role in producing smart textiles, paving the way for advancements in functionality and user experiences.
As we embrace sustainability, digitalization, customization, collaboration, automation, and smart textiles, the textile industry is poised for a future defined by innovation and efficiency. Explore Svegea’s innovative solutions to stay ahead in the evolving textile landscape and drive your business toward success.
The textile industry is undergoing transformative changes driven by trends around sustainability, automation, customization, and circularity. Leading machinery manufacturers offer cutting-edge solutions to help textile producers capitalize on these powerful market shifts.
Sustainability Imperative
Environmental consciousness is fueling the demand for eco-friendly textiles, currently, a global textile trend that we cannot ignore. Innovative machinery enables sustainable manufacturing practices like energy efficiency and waste reduction, minimizing environmental impact while maintaining competitive operations.
Automation & Industry 4.0
Principles like robotics, AI, and IoT are optimizing production through automation. Advanced textile machinery seamlessly integrates these technologies to streamline operations, boost productivity, and reduce costs – keeping manufacturers at the forefront of the digital revolution.
Customization & Diversification
Evolving consumer tastes favor personalized products and unique experiences. Flexible machinery allows for customized, diverse offerings tailored to changing market demands.
Circular Economy Transition
Resource efficiency is paramount, with textile circularity reducing waste. Circular knitting machines and recycling technologies enable closed-loop supply chains by repurposing waste into new materials.
As these trends reshape the global landscape, machinery manufacturers position textile producers for success. By adopting innovative solutions for sustainability, automation, customization, and circularity, industry leaders can drive sustainable growth and gain a lasting competitive edge.
For inquiries, brochures, or further information about Svegea of Sweden’s cutting-edge textile machinery, visit our contact page.