In the ever-evolving textile industry, fabric inspection has always been a critical yet challenging task. Ensuring the highest quality of fabrics is essential for maintaining brand reputation and customer satisfaction. However, traditional methods of fabric inspection are often time-consuming and prone to human error. This is where artificial intelligence (AI) steps in, revolutionizing the way we approach fabric inspection.
The Need for Advanced Fabric Inspection
As someone deeply involved in the textile industry, I have witnessed firsthand the limitations of manual fabric inspection. The process is labor-intensive and can miss subtle defects that affect the final product’s quality. With the increasing demand for flawless fabrics, there is a pressing need for more efficient and accurate inspection methods.
How AI Transforms Fabric Inspection
AI technology has brought a significant shift in fabric inspection processes. By integrating AI, companies like Svegea of Sweden are setting new standards in quality control. AI systems use high-resolution cameras and sophisticated algorithms to detect defects that human eyes might overlook. These systems can identify issues such as misweaves, pattern irregularities, and color deviations with remarkable precision.
One of the most impressive aspects of AI in fabric inspection is its ability to process vast amounts of fabric quickly. What used to take hours can now be done in minutes, significantly speeding up the production cycle and reducing labor costs. This efficiency not only enhances productivity but also ensures that only top-quality fabrics reach the market.
Svegea of Sweden: Leading the Way
Svegea of Sweden has been at the forefront of integrating AI into fabric inspection. Their innovative approach combines advanced technology with industry expertise to deliver unparalleled results. For instance, their latest fabric inspection machine, equipped with AI capabilities, can scan and analyze fabrics in real-time, ensuring that any defects are immediately identified and addressed.
This technology is a game-changer for the textile industry. By automating the inspection process, Svegea of Sweden not only improves accuracy but also frees up human inspectors to focus on more complex tasks that require a human touch. This blend of AI and human expertise creates a more efficient and effective inspection process.
Benefits of AI in Fabric Inspection
The benefits of using AI for fabric inspection are manifold. Firstly, it enhances accuracy. AI systems can detect even the smallest defects, ensuring that only the best fabrics make it to the market. This level of precision is difficult to achieve with manual inspection alone.
Secondly, AI-driven inspection systems are incredibly efficient. They can process large volumes of fabric quickly, reducing the time required for inspection and speeding up the overall production process. This efficiency translates into cost savings for manufacturers, as they can produce more in less time.
Moreover, AI systems are consistent. Unlike human inspectors, who may have varying levels of attention and expertise, AI systems provide uniform quality control. This consistency is crucial for maintaining high standards across all products.
Real-World Applications
The real-world applications of AI in fabric inspection are impressive. For example, companies using AI technology have reported significant reductions in defect rates and improvements in overall product quality. This technology is not just a theoretical concept; it is being used successfully in the industry today.
Svegea of Sweden’s AI-powered fabric inspection machines is a testament to this success. By leveraging AI, they have been able to enhance their inspection processes, ensuring that their fabrics meet the highest quality standards. This commitment to quality has helped them build a strong reputation in the industry.
The Future of Fabric Inspection
Looking ahead, the future of fabric inspection lies in further advancements in AI technology. As AI systems become more sophisticated, they will be able to detect even more subtle defects and provide even greater accuracy. This will set new benchmarks for quality control in the textile industry.
Additionally, the integration of AI with other technologies, such as the Internet of Things (IoT) and machine learning, will open up new possibilities for fabric inspection. For instance, IoT-enabled sensors can provide real-time data on fabric conditions, which AI systems can analyze to predict potential defects before they occur.
Revolutionizing the Fabric Inspection Technology
AI technology is revolutionizing fabric inspection, making it more accurate, efficient, and consistent. Companies like Svegea of Sweden are leading the way, demonstrating the immense potential of AI in the textile industry. By embracing this technology, manufacturers can ensure that their fabrics meet the highest quality standards, enhancing their reputation and customer satisfaction.
If you are interested in learning more about how AI can transform your fabric inspection processes, visit Svegea of Sweden’s fabric inspection page. Discover how their innovative solutions can help you achieve unparalleled quality control in your textile production.
Preserving history, one fabric at a time! Discover why textile conservation is crucial to safeguarding the past for future generations.
Textile conservation is a specialized field dedicated to preserving historical fabrics that offer a tangible connection to our past. These textiles aren’t just pieces of cloth; they tell stories of cultures, traditions, and technological advancements. This blog will explore the significance of textile conservation, the techniques involved, and how modern textile machines contribute to this delicate preservation process.
The Importance of Textile Conservation
Historical fabrics offer invaluable insights into social, economic, and cultural histories. Without proper conservation, these artifacts would deteriorate, erasing important chapters of human history. Textile conservation ensures that future generations can continue studying and appreciating these pieces of the past.
Cultural Significance
Textiles often hold deep cultural importance. Traditional garments showcase unique weaving techniques and patterns, offering glimpses into the identities of diverse communities. Preserving these fabrics helps protect cultural heritage, ensuring it remains intact for future generations to learn from.
Educational Value
Historical fabrics serve as powerful educational tools. Researchers and students can study ancient techniques, materials, and designs that have shaped modern innovations in textiles. By conserving these textiles, we preserve this knowledge for future generations to explore.
Techniques in Textile Conservation
Preserving delicate fabrics requires specialized techniques tailored to the fabric’s age, condition, and historical value.
- Cleaning and Stabilization – One of the first steps in textile conservation is gentle cleaning to remove dirt and contaminants. Stabilization follows, reinforcing fragile areas to prevent further damage while maintaining the fabric’s integrity.
- Repair and Restoration – In some cases, conservators repair damaged textiles, ensuring that repairs are as discreet as possible. Restoration work aims to return the fabric to its original appearance, allowing it to tell its full story while maintaining authenticity.
The Role of Textile Machines
Modern textile machines play a pivotal role in helping conservators perform these intricate tasks with precision.
- Advanced Weaving Machines – These machines can replicate historical weaving techniques, making it easier to create seamless patches that blend with the original fabric. This ensures that repairs remain nearly invisible, preserving the authenticity of the textile.
- Cleaning and Drying Equipment – Specialized cleaning and drying machines help protect fragile fabrics by providing a controlled environment. These machines ensure that delicate textiles are handled with care during every step of the cleaning process.
Svegea of Sweden: Precision Machines for Conservation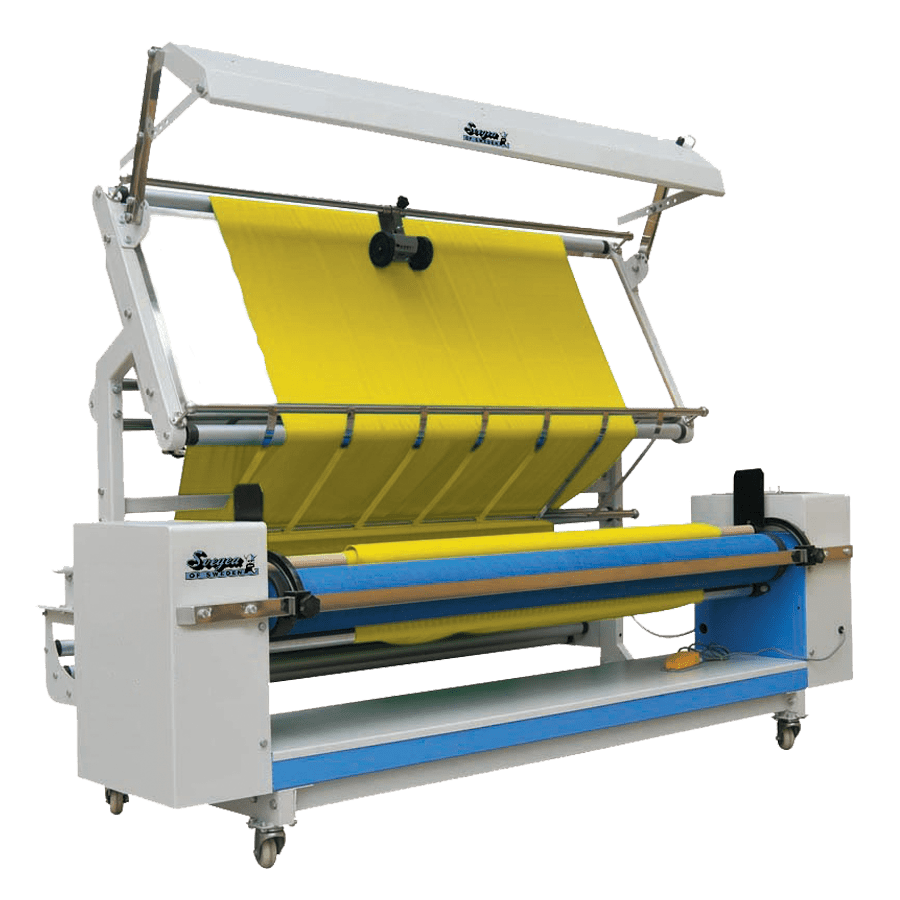
Svegea of Sweden provides advanced textile machines that play a vital role in modern textile manufacturing and quality control. Their equipment, including the Fabric Inspection Machine CMI 180, is designed for precision and delicate handling, ensuring high-quality fabrics. While primarily used for quality control, these machines support the broader textile industry, which includes conservation efforts by ensuring that only the best materials are used in preservation projects.
Case Studies in Textile Conservation
Several high-profile conservation projects highlight the importance and success of textile conservation:
- The Bayeux Tapestry: An 11th-century masterpiece, the Bayeux Tapestry underwent meticulous cleaning and stabilization, preserving it for generations to come.
- The Shroud of Turin: This significant religious artifact benefited from advanced textile conservation techniques, ensuring its continued preservation.
Challenges in Textile Conservation
Textile conservation faces several challenges, including the fragility of fabrics and environmental threats such as humidity, light, and temperature.
Fabric Fragility
Handling fragile textiles requires expert knowledge and specialized equipment to avoid causing further damage during the conservation process.
Environmental Factors
Conservators must constantly manage factors such as humidity and light exposure, which can accelerate the deterioration of historical fabrics. Controlled environments are essential for long-term preservation.
The Future of Textile Conservation
Technological advancements and growing awareness promise a bright future for textile conservation.
Technological Innovations
Cutting-edge technologies like 3D scanning and digital imaging allow conservators to analyze fabrics in unprecedented detail. These innovations are transforming preservation techniques, enabling conservators to develop more effective methods.
Increased Awareness
Growing public and institutional awareness of the importance of textile conservation has led to increased funding and support for preservation projects. As more people understand the value of preserving these historical fabrics, the future of textile conservation looks bright.
Preserving Cultural Heritage
Textile conservation is essential for preserving our cultural heritage and ensuring future generations have access to these invaluable artifacts. By using advanced techniques and modern machines like those from Svegea of Sweden, conservators can safeguard these fabrics for years to come. As we continue to innovate and raise awareness, textile conservation will thrive, preserving history—one fabric at a time.
For expert textile machines, contact Svegea of Sweden for precision solutions tailored to your conservation needs.
Choosing the right textile machinery can be a daunting task, especially with the plethora of options available in the market. The decision impacts your production efficiency, product quality, and overall business profitability. Here are some key tips to help you navigate this critical process.
1. Understand Your Production Needs
Before investing in textile machinery, it’s crucial to understand your specific production needs. Different types of machinery serve various purposes, from weaving and knitting to dyeing and finishing. Determine the scale of your operations, the types of textiles you produce, and your production goals. This understanding will guide your choice of machinery that best suits your requirements.
2. Evaluate Technology and Features
Modern textile machinery comes with a range of advanced technologies and features designed to enhance productivity and quality. Look for machines that offer automation, precision control, and energy efficiency. For instance, Svegea of Sweden offers cutting-edge machinery equipped with the latest technology, ensuring high efficiency and minimal waste. Our products are known for their durability and innovative features.
3. Consider Quality and Reliability
Quality and reliability are paramount when choosing textile machinery. Investing in high-quality machines may come with a higher initial cost, but it ensures long-term performance and fewer breakdowns. Research and compare different brands, read reviews, and consider the manufacturer’s reputation. Modesty aside, our brand has a proven track record of producing reliable and high-quality textile machinery.
4. Assess After-Sales Support and Maintenance
After-sales support and maintenance services are crucial for the smooth operation of textile machinery. Ensure that the manufacturer offers comprehensive support, including installation, training, and regular maintenance services. We provide excellent customer support and maintenance services, ensuring that your machinery operates optimally.
5. Analyze Cost and Return on Investment (ROI)
While the cost of textile machinery is a significant factor, it’s essential to consider the return on investment (ROI). A more expensive machine with advanced features and higher efficiency can lead to cost savings in the long run. Calculate the total cost of ownership, including maintenance and operational costs, and compare it with the expected benefits. Opt for machines that offer the best value for money.
6. Environmental Considerations
Sustainability is a growing concern in the textile industry. Choose machinery that is energy-efficient and environmentally friendly. Machines that reduce water and chemical usage, minimize waste, and consume less energy are ideal. This Swedish textile company is known for producing sustainable textile machinery that aligns with eco-friendly production practices.
7. Compatibility with Existing Systems
Ensure that the new machinery is compatible with your existing systems and processes. Incompatibility can lead to production delays and additional costs. Consult with the manufacturer or a technical expert to evaluate the integration process. A company that offers flexible machinery solutions that can be seamlessly integrated into various production setups, should be the right choice.
Explore Svegea of Sweden’s Textile Machinery
Choosing the right textile machinery is a critical decision that impacts your production efficiency and product quality. By considering factors such as your production needs, technology and features, quality, after-sales support, cost, environmental impact, and compatibility, you can make an informed choice. Svegea of Sweden’s innovative machinery solutions are designed to meet diverse production requirements while ensuring high efficiency and sustainability.
Curious about how we can elevate your textile production process? Visit our product page for more information and start your journey towards optimal textile production today.
In the quest for sustainable fashion, choosing the right fabrics is crucial. Eco-friendly fabric choices not only reduce environmental impact but also promote ethical production practices. This guide explores some of the best sustainable fabrics and their benefits.
Understanding Eco-Friendly Fabrics
Eco-friendly fabrics are made from natural, renewable, or recycled materials that have a lower environmental footprint compared to conventional fabrics. These fabrics are produced using methods that minimize water usage, chemical treatments, and energy consumption.
Popular Eco-Friendly Fabrics
- Organic Cotton: Grown without harmful pesticides and synthetic fertilizers, organic cotton is a popular choice for sustainable fashion. It is soft, breathable, and biodegradable.
- Bamboo: Bamboo fabric is made from the pulp of bamboo grass, which grows quickly and requires minimal water and pesticides. It is naturally antibacterial and moisture-wicking.
- Hemp: Hemp is a highly sustainable crop that requires little water and no pesticides. It produces a durable and versatile fabric that is perfect for various types of clothing.
- Recycled Polyester: Made from recycled plastic bottles, recycled polyester reduces waste and conserves resources. It is often used in activewear due to its durability and moisture-wicking properties.
- Tencel (Lyocell): Tencel is a sustainable fabric made from wood pulp sourced from responsibly managed forests. It is biodegradable, soft, and has a silky feel.
The Environmental Impact
Choosing eco-friendly fabrics significantly reduces the environmental impact of fashion production. These fabrics require fewer resources, produce less waste, and are often biodegradable or recyclable. By opting for sustainable fabrics, designers and consumers can contribute to a greener planet.
Economic Benefits
Sustainable fabrics are not only good for the environment but also for business. As consumers become more environmentally conscious, there is a growing demand for eco-friendly products. Brands that use sustainable fabrics can attract a loyal customer base willing to pay a premium for ethical and eco-friendly fashion.
Challenges and Innovations
While eco-friendly fabrics offer many benefits, there are challenges in their production and adoption. The cost of sustainable materials can be higher, and the supply chain may be less established compared to conventional fabrics. However, innovations in textile technology and increased consumer awareness are helping to overcome these challenges.
Success Stories
Many brands are leading the way in sustainable fashion by using eco-friendly fabrics. For example, Patagonia uses recycled polyester in its clothing, and Stella McCartney incorporates organic cotton and Tencel in her designs. These brands demonstrate that sustainability and style can coexist.
The Future of Fashion
The future of fashion lies in sustainability. By choosing eco-friendly fabrics, the industry can reduce its environmental footprint and create a more ethical production process. As more brands and consumers embrace sustainable practices, we can look forward to a fashion industry that is both stylish and environmentally responsible.
Cutting Edge Technology
Svegea of Sweden provides cutting-edge technology that complements the zero waste cutting process, enabling manufacturers to take their sustainability initiatives to the next level. With the Euro Collarette Cutter, Svegea offers a solution that not only minimizes fabric waste but also boosts production efficiency and cost-effectiveness. Euro Collarette Cutters are designed to optimize fabric cutting processes, providing highly efficient solutions that align with zero waste cutting principles. These machines are integral for manufacturers aiming to reduce fabric waste, streamline production, and meet sustainability goals.
Key Features of Svegea’s Euro Collarette Cutters:
- Precision Cutting: Euro Collarette Cutters are renowned for their precise, consistent cutting ability, reducing the amount of fabric waste that typically results from inefficient manual cutting techniques.
- Flexibility in Fabric Handling: These machines are capable of handling various fabric types and thicknesses, making them versatile for different garment production needs. This flexibility ensures minimal waste regardless of the fabric used, supporting zero waste pattern cutting.
- Automation and Efficiency: The advanced automation technology integrated into Svegea’s cutters allows for higher production speeds while maintaining precision. Automation reduces the likelihood of human error, further minimizing material waste.
- Sustainability-Driven Design: Svegea develops its cutting machines with a strong focus on sustainability, ensuring that they minimize fabric waste to nearly zero. These solutions seamlessly integrate into eco-conscious production environments, allowing manufacturers to adopt greener practices while enhancing efficiency.
- Cost Savings: By maximizing fabric use, these machines reduce raw material costs, contributing to both economic and environmental benefits for manufacturers adopting zero waste practices.
Contact us to explore how Svegea’s Euro Collarette Cutters can transform your production line for a more sustainable future.
In a world where sustainability is becoming more than a buzzword, the fashion industry is undergoing a significant transformation. One of the most innovative and impactful changes is the adoption of zero waste pattern cutting. This method not only revolutionizes the way garments are produced but also addresses the environmental concerns associated with traditional fashion practices.
Understanding Zero Waste Pattern Cutting
Zero waste pattern cutting is a design technique that aims to eliminate fabric waste in the creation of garments. Traditional garment production often results in approximately 15-20% of fabric waste due to the inefficient placement of patterns on the fabric. This discarded material often ends up in landfills, contributing to environmental pollution.
In contrast, zero waste pattern cutting meticulously plans the layout of each piece of fabric, ensuring that every inch is utilized. This approach can involve intricate designs, geometric shapes, and innovative sewing techniques to fit the pieces together like a puzzle. The result is a garment that uses all the fabric with minimal to no waste.
The Environmental Impact
The fashion industry is notorious for its environmental footprint. From water consumption to carbon emissions, the production of clothing has significant impacts on the planet. Zero waste pattern cutting offers a practical solution to one of these issues: fabric waste.
By reducing fabric waste, this method helps in conserving resources. It means fewer raw materials are needed, reducing the demand for water, energy, and chemicals involved in fabric production. Additionally, less waste means fewer textiles end up in landfills, decreasing environmental pollution.
Economic Benefits
While the environmental benefits of zero waste pattern cutting are clear, the economic advantages are equally compelling. For designers and manufacturers, fabric is a significant cost. By maximizing fabric usage, zero waste techniques can lead to substantial cost savings.
Moreover, as consumers become more conscious of sustainability, there is a growing market for eco-friendly products. Brands that adopt zero waste practices can attract environmentally conscious customers, willing to pay a premium for sustainable fashion. This shift not only helps the planet but also makes good business sense.
Challenges and Innovations
Despite its many benefits, zero waste pattern cutting is not without its challenges. The method requires a high level of skill and creativity. Designers must rethink the way they approach garment construction, often needing to create entirely new patterns and techniques.
However, this challenge has spurred innovation in the industry. Designers are experimenting with modular designs, where pieces can be rearranged and used in multiple ways. Digital tools and software are also being developed to aid in the creation of zero waste patterns, making the process more accessible to a broader range of designers.
Success Stories
Many brands and designers are already making significant strides in zero waste fashion. For instance, designers like Timo Rissanen and Holly McQuillan are pioneers in this field, pushing the boundaries of what is possible with zero waste pattern cutting. Their work not only showcases the potential of this method but also inspires others in the industry to follow suit.
Brands like Tonlé and Daniel Silverstein (Zero Waste Daniel) have built their entire business models around zero waste principles. They demonstrate that sustainability and style can go hand in hand, offering chic and modern designs that do not compromise on environmental values.
The Future of Fashion
As the fashion industry continues to evolve, the importance of sustainable practices cannot be overstated. Zero waste pattern cutting represents a significant step forward in this journey. It challenges the status quo, pushing designers and manufacturers to think creatively and responsibly.
The future of fashion lies in innovation and sustainability. By adopting zero waste techniques, the industry can reduce its environmental footprint, create economic opportunities, and cater to a growing market of eco-conscious consumers. As more brands embrace this method, we can look forward to a fashion industry that not only looks good but does good for the planet.
Svegea of Sweden: Revolutionizing Zero Waste with Advanced Technology
One notable brand making strides in the realm of zero waste pattern cutting is Svegea of Sweden. Known for their advanced cutting machinery, Svegea offers innovative solutions designed to maximize fabric utilization. Their machines not only enhance precision but also significantly reduce waste, aligning perfectly with the zero waste philosophy. By incorporating Svegea’s technology, designers can seamlessly integrate zero waste techniques into their production process.
Curious about how Svegea of Sweden can elevate your zero waste pattern cutting process? Visit our contact page for more information on our cutting-edge machinery and start your journey towards a more sustainable future today.
Ever wondered how fabrics impact your mood? The textures of the textiles we surround ourselves with can significantly influence our emotions and behavior. This article delves into the fascinating psychology of fabric textures and how they can shape our daily experiences.
The Power of Fabric Textures
Fabric texture refers to the surface quality of a fabric, which can be smooth, rough, soft, or stiff. Different textures evoke different emotional responses.
Smooth Textures: Fabrics like silk, satin, and cotton have smooth textures. These materials are often associated with luxury and comfort. Wearing smooth fabrics can make you feel more relaxed, elegant, and confident. They’re perfect for special occasions or when you want to pamper yourself.
Rough Textures: Fabrics like wool and raw silk are examples of rough textures. These materials can evoke feelings of ruggedness, durability, and strength. Wearing rough-textured fabrics can make you feel more grounded and resilient. They’re great for casual, everyday wear or outdoor activities.
Soft Textures: Fabrics such as velvet are incredibly soft. These fabrics are associated with warmth, comfort, and nurturing. Wearing soft, textured fabrics can make you feel cozy and secure, making them ideal for relaxing at home or during the colder months.
Stiff Textures: Fabrics like organza have a stiff texture. These fabrics often convey formality and structure. Wearing stiff fabrics can make you feel more disciplined and poised. They’re suitable for formal events or professional settings.
The Influence of Fabric Colors
Colors are powerful psychological tools that can influence our emotions and perceptions. Different colors can have varying effects on our mood.
Red: Red is a bold and stimulating color. It is often associated with passion, energy, and excitement. Wearing red can make you feel more confident and assertive. It’s a great choice for events where you want to stand out and make a strong impression.
Blue: Blue is a calming and soothing color, often linked to feelings of tranquility, trust, and stability. Wearing blue can help you feel more relaxed and at peace. It’s ideal for situations where you need to stay calm and composed, such as job interviews or exams.
Yellow: Yellow is a bright and cheerful color. It is associated with happiness, optimism, and creativity. Wearing yellow can lift your spirits and make you feel more joyful and energetic. It’s perfect for social gatherings or creative endeavors.
Green: Green is a refreshing and harmonious color. It represents nature, balance, and growth. Wearing green can make you feel more refreshed and rejuvenated.
Combining Textures and Colors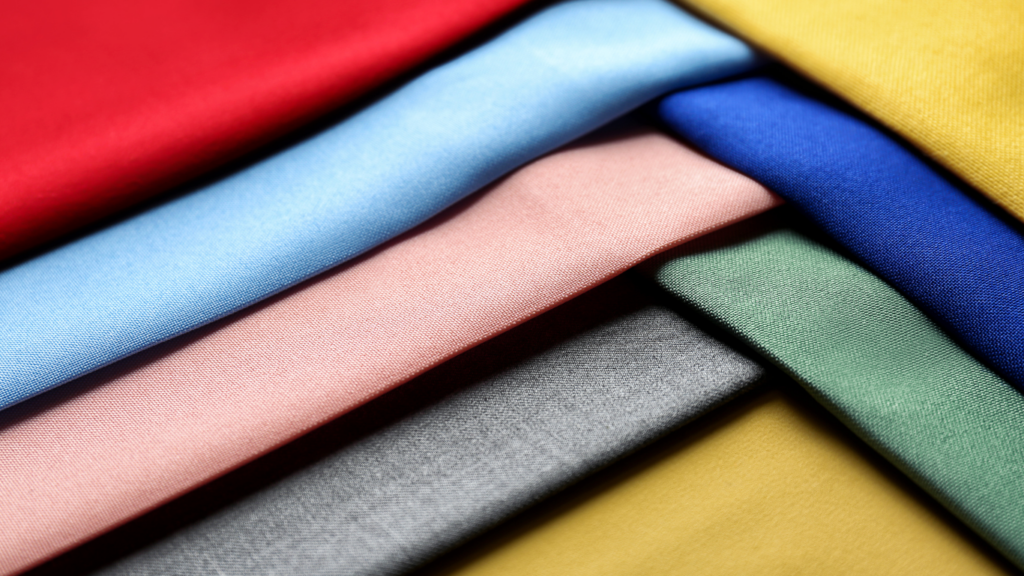
The combination of textures and colors can create a powerful impact on your mood and behavior. For instance, a smooth, blue silk dress can make you feel both elegant and calm, while a rough, red wool sweater can evoke feelings of strength and confidence. Understanding how these elements work together can help you make more informed choices about your wardrobe and home decor.
Svegea of Sweden: Innovating Textile Machinery
Svegea of Sweden is at the forefront of textile machinery innovation. Their advanced fabric-cutting machines ensure precision and efficiency, making it easier for designers to create garments that not only look good but also feel good. By investing in high-quality machinery from Svegea, manufacturers can produce textiles that meet the psychological needs of their customers.
Svegea leads the textile industry with its quality and innovation. Their machines cut various fabrics with utmost precision. This attention to detail helps create garments that provide the desired emotional and psychological benefits to the wearer.
A Fascinating Field
The psychology of fabric is a fascinating field that highlights the significant impact that textures and colors can have on our moods and behavior. By understanding these effects, we can make more informed choices about the fabrics we wear and surround ourselves with. Whether you’re looking to feel more confident, relaxed, or joyful, the right fabric can make all the difference.
For manufacturers and designers, investing in high-quality textile machinery from Svegea of Sweden can help ensure that your products meet the psychological needs of your customers. To learn more about Svegea’s innovative solutions, visit their contact page.
Explore the world of fabrics and discover how the textures and colors you choose can transform your mood and behavior. Make informed choices and experience the psychological benefits of the right textiles today!
In the dynamic world of textile manufacturing, automation is a cornerstone of innovation, driving unprecedented efficiency, precision, and sustainability. As an expert with over two decades of experience in textile automation, we have witnessed firsthand the transformative power of these technologies. Today, we’ll explore how automation is reshaping the fabric of our industry.
The Evolution of Textile Automation
The journey from hand-spun fibers to today’s high-tech production lines tells a story of relentless innovation. Early mechanization during the Industrial Revolution laid the groundwork, but modern automation has catapulted us into a new era of manufacturing excellence.
Key milestones include:
1. 1960s-1970s: Introduction of computer-controlled looms
2. 1980s-1990s: Development of robotic systems for material handling
3. 2000s-2010s: Integration of AI and machine learning in quality control
4. 2020s and beyond: Emergence of fully automated, smart textile factories
Core Areas Transformed by Automation
Spinning: Precision at Lightning Speeds
Modern spinning systems, such as rotor and air-jet technologies, have revolutionized yarn production. These systems can produce yarn up to 20 times faster than traditional ring spinning, with unparalleled consistency.
Weaving: Intelligent Looms for Flawless Fabrics
Today’s computerized looms are marvels of engineering. There are machines for example that use real-time adaptive tension control to adjust warp tension on the fly, ensuring fabric quality remains consistent even as conditions change during production. This level of precision was unthinkable just a decade ago.
Dyeing and Finishing: Sustainability Meets Efficiency
Automated dyeing and finishing processes have dramatically reduced water and energy consumption while improving color consistency. Digital textile printing, exemplified by machines can print complex designs directly onto fabric at up to 1,000 m²/hour, revolutionizing small-batch and customized production.
Spotlight on Innovation: Svegea’s EC 450 XF Collarette Cutting System
The EC 450 XF Collarette Cutting System by Svegea represents the cutting edge of textile automation. As the winner of the Texprocess Americas 2023 Innovation Award, this system exemplifies how targeted automation can solve specific industry challenges.
Key features include:
– Multi-material compatibility for unparalleled versatility
– Precision cutting with minimal waste
– Rapid changeover times, boosting overall productivity
The EC 450 XF doesn’t just cut fabric; it redefines efficiency in garment manufacturing. For manufacturers looking to stay competitive, systems like this are not just beneficial—they’re essential.
The Tangible Benefits of Automation
1. Quality Assurance: Automated systems consistently produce high-quality textiles, reducing defects by up to 90% compared to manual processes.
2. Increased Productivity: Modern automated lines can operate 24/7, increasing output by 200-300% over traditional methods.
3. Cost Reduction: While initial investment is significant, automated systems can reduce labor costs by 40-60% and material waste by 20-30% over their lifetime.
4. Customization at Scale: Automation enables quick changeovers, making small-batch and customized production economically viable.
5. Enhanced Safety: Automation minimizes human exposure to hazardous processes, reducing workplace accidents by up to 80% in some facilities.
Overcoming Implementation Challenges
While the benefits of automation are clear, implementation comes with challenges:
1. Initial Investment: The upfront cost of automation can be substantial. However, ROI typically occurs within 2-5 years, depending on the scale of implementation.
2. Workforce Transition: Shifting to automated systems requires retraining staff. Forward-thinking companies are investing in upskilling programs to transition workers into higher-value roles.
3. System Integration: Ensuring new automated systems work seamlessly with existing processes is crucial. Careful planning and phased implementation can mitigate disruptions.
The Future of Textile Automation
Looking ahead, several trends will shape the future of textile automation:
1. AI and Machine Learning: These technologies will enable predictive maintenance and real-time quality control, further improving efficiency and reducing downtime.
2. Internet of Things (IoT): Connected devices will create smart factories where every aspect of production is monitored and optimized in real-time.
3. Sustainable Automation: Future systems will focus even more on reducing environmental impact, with closed-loop water systems and energy-efficient processes.
4. Collaborative Robotics: Cobots will work alongside humans, handling repetitive tasks while allowing human workers to focus on high-value activities.
Embracing the Automated Future
Automation in textile manufacturing isn’t just about replacing human labor—it’s about augmenting human capabilities, driving innovation, and creating a more sustainable, efficient industry. As we look to the future, it’s clear that automation will play an increasingly central role in shaping the textiles of tomorrow.
For manufacturers, the message is clear: embrace automation or risk being left behind. The future of textiles is automated, and that future is now.
To explore cutting-edge automation solutions like Svegea’s EC 450 XF Collarette Cutting System, contact us now! For those ready to take the next step in their automation journey, now is the time to act.
The textile manufacturing industry is undergoing a significant transformation. As we move into 2025, several trends are shaping the future of this dynamic sector. From sustainable practices to advanced technologies, the landscape is evolving rapidly. Let’s explore the top trends in textile manufacturing for 2024 and 2025.
1. Sustainable Practices
Sustainability is no longer a buzzword; it’s a necessity. Textile manufacturers are increasingly adopting eco-friendly practices to reduce their environmental footprint. This includes using organic materials, recycling waste, and implementing energy-efficient processes. According to the World Economic Forum, sustainable practices in textile manufacturing can significantly reduce carbon emissions and water usage.
2. Advanced Technologies
The integration of advanced technologies is revolutionizing textile manufacturing. Automation, artificial intelligence (AI), and the Internet of Things (IoT) are enhancing efficiency and productivity. For instance, AI-driven machines can predict maintenance needs, reducing downtime and increasing output. The International Textile Manufacturers Federation highlights that these technologies are crucial for staying competitive in the global market.
3. Customization and Personalization
Consumers today demand unique and personalized products. Textile manufacturers are leveraging digital printing and other technologies to offer customized solutions. This trend is particularly evident in the fashion industry, where personalized clothing is gaining popularity. A report by McKinsey & Company suggests that customization will be a key driver of growth in the textile sector.
4. Smart Textiles
Smart textiles, also known as e-textiles, are gaining traction. These textiles have embedded sensors and electronics that can monitor health, track fitness, and even change color. The potential applications are vast, ranging from healthcare to sportswear. According to TechCrunch, the smart textiles market is expected to grow exponentially in the coming years.
5. Ethical Labor Practices
Consumers are becoming more conscious of the ethical implications of their purchases. As a result, textile manufacturers are focusing on fair labor practices and ensuring safe working conditions. This shift is not only ethical but also beneficial for brand reputation. The Fair Labor Association provides guidelines and resources for companies aiming to improve their labor practices.
Spotlight on Svegea of Sweden
Svegea of Sweden is a notable player in the textile manufacturing industry. Known for their innovative solutions, Svegea offers advanced slitting and cutting machines that enhance efficiency and precision. Their commitment to quality and sustainability sets them apart in the market. While not overtly promotional, it’s worth noting how companies like Svegea are contributing to the industry’s evolution.
Exciting Changes
The textile manufacturing industry is poised for exciting changes in 2025. From sustainable practices to advanced technologies, the trends shaping this sector are both innovative and impactful. By staying informed and adapting to these trends, manufacturers can thrive in a competitive landscape.
For innovative and sustainable textile machinery, contact Svegea of Sweden. Our advanced solutions can help you stay ahead in the evolving textile industry.
Textile innovation is a fascinating journey that transforms raw ideas into tangible fabrics. This process involves creativity, technology, and a deep understanding of materials. In this blog, we will explore the stages of textile innovation, highlight the role of Svegea of Sweden, and provide insights into how modern machinery is revolutionizing the industry.
The Birth of an Idea
Every textile innovation begins with a concept. Designers and engineers brainstorm to create new fabrics that meet specific needs. Whether it’s for fashion, sports, or industrial use, the initial idea is crucial. This stage involves extensive research and development to ensure the concept is viable.
Research and Development
Research and development (R&D) are at the heart of textile innovation. Scientists and engineers work together to test new materials and techniques. They experiment with different fibers, dyes, and weaving methods to create fabrics that are not only functional but also aesthetically pleasing. This phase is critical as it lays the foundation for the entire process.
Prototyping and Testing
Once the concept is solidified, the next step is prototyping. This involves creating a small batch of the fabric to test its properties. Prototyping allows designers to see how the fabric performs in real-world conditions. They can make adjustments to improve durability, comfort, and appearance.
Importance of Testing
Testing is an essential part of the innovation process. Fabrics are subjected to various tests to ensure they meet industry standards. These tests include checking for strength, flexibility, and resistance to wear and tear. By rigorously testing prototypes, manufacturers can guarantee the quality of the final product.
Production and Manufacturing
After successful prototyping and testing, the fabric moves to the production phase. This is where innovative machinery plays a significant role. Companies like Svegea of Sweden provide state-of-the-art textile machinery that enhances efficiency and precision in manufacturing.
Role of Svegea of Sweden
Svegea of Sweden is a leader in textile machinery innovation. Their machines are designed to handle complex weaving and knitting processes with ease. By incorporating advanced technology, Svegea ensures that fabrics are produced with the highest quality standards. Their machinery is known for its reliability and efficiency, making them a preferred choice for many textile manufacturers.
Sustainability in Textile Innovation
In today’s world, sustainability is a key consideration in textile innovation. Manufacturers are increasingly focusing on eco-friendly materials and processes. This includes using organic fibers, reducing water consumption, and minimizing waste. Sustainable practices not only benefit the environment but also appeal to conscious consumers.
Eco-Friendly Materials
The use of eco-friendly materials is a growing trend in the textile industry. Organic cotton, bamboo, and recycled polyester are some sustainable fibers. These materials are not only environmentally friendly but also offer excellent performance characteristics. By choosing sustainable options, manufacturers can reduce their environmental footprint.
The Future of Textile Innovation
The future of textile innovation looks promising with continuous advancements in technology. Smart fabrics, which can monitor health or change color, are becoming a reality. Additionally, 3D printing is opening new possibilities for custom-made textiles. As technology evolves, the potential for innovation in textiles is limitless.
Embracing New Technologies
Embracing new technologies is essential for staying competitive in the textile industry. Companies that invest in advanced machinery and innovative processes are better positioned to meet the demands of modern consumers. Svegea of Sweden, with its cutting-edge textile machinery, is at the forefront of this technological revolution.
An Exciting Process
From concept to fabric, the journey of textile innovation is a complex and exciting process. It involves creativity, rigorous testing, and the use of advanced machinery. Companies like Svegea of Sweden play a crucial role in this journey by providing innovative solutions that enhance production efficiency and quality.
If you want to learn more about how innovative textile machinery can transform your production process, contact Svegea of Sweden today. Their expertise and state-of-the-art machines can help you stay ahead in the competitive textile industry.
The textile industry has always been a pioneer in technological advancements. From the spinning jenny to modern automated looms, the sector has continually evolved. Today, the integration of Artificial Intelligence (AI) into textile machines marks the latest leap forward, offering unparalleled efficiency, precision, and productivity. This article delves into how AI textile machines are revolutionizing the industry and highlights a cutting-edge product from Svegea of Sweden.
The Rise of AI in Textile Manufacturing
AI is no longer a futuristic concept; it is now a vital component of the manufacturing sector, especially in textiles. The industry is swiftly adopting AI technologies to enhance production processes, improve product quality, and reduce waste. AI-powered machines can analyze vast amounts of data in real time, enabling more informed decision-making and streamlined operations.
AI’s ability to learn from data and make real-time adjustments has transformed textile manufacturing. These machines can predict when a process needs adjustment, reducing downtime and boosting overall efficiency. For instance, AI can optimize machine settings based on the fabric type, ensuring each material is handled with utmost care and precision.
Reducing Waste and Enhancing Sustainability
One of the most significant benefits of AI-integrated textile machines is their ability to minimize waste. Traditional manufacturing often results in excess material being discarded, increasing costs and environmental impact. AI can significantly reduce this waste by optimizing cutting and sewing processes.
AI algorithms can analyze fabric patterns to determine the most efficient cutting method, minimizing leftover scraps. This not only reduces waste but also lowers costs for manufacturers. Additionally, AI can monitor fabric quality throughout production, identifying and correcting defects early.
Reducing waste also supports the industry’s sustainability efforts. As demand for eco-friendly products grows, manufacturers face increasing pressure to adopt sustainable practices. AI textile machines play a crucial role in this shift by enabling more efficient resource use and reducing the carbon footprint of textile production.
Enhancing Productivity with AI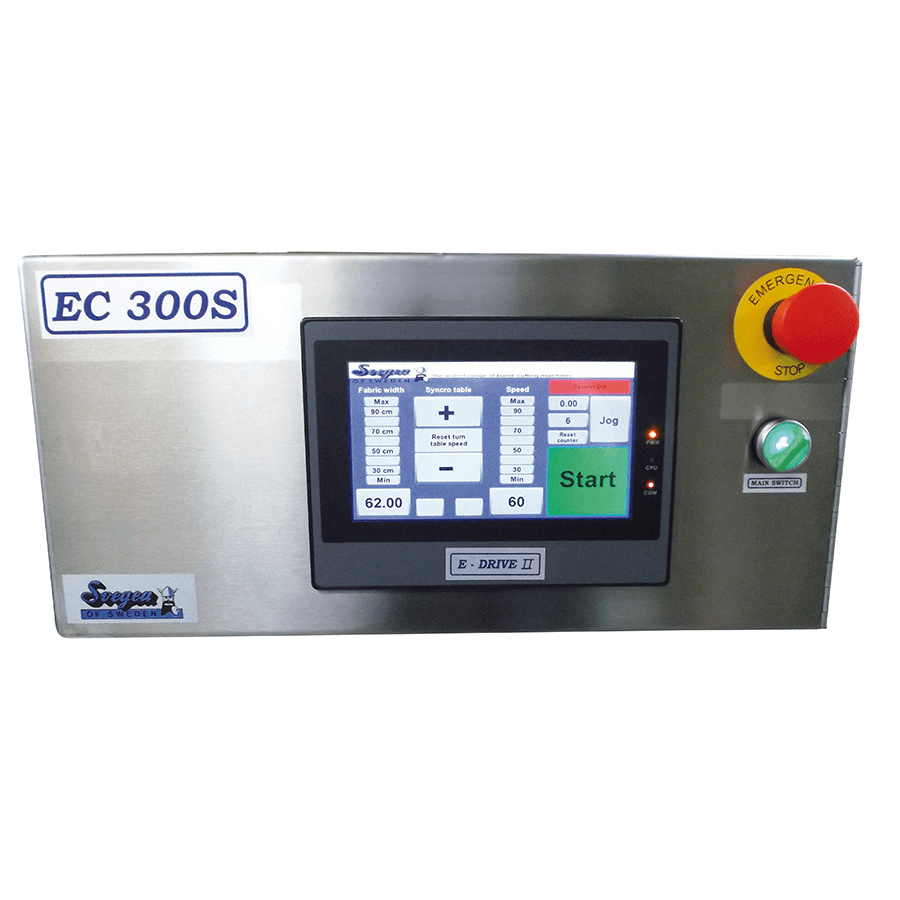
Productivity is a key metric in any manufacturing environment, and the textile industry is no exception. AI-integrated machines are designed to maximize output without compromising quality. By automating routine tasks, these machines free up human workers to focus on more complex, value-added activities.
For example, AI can automate the inspection process, quickly identifying defects that human inspectors might miss. This speeds up the production line and ensures only the highest-quality products reach the market. Additionally, AI can predict machine failures, allowing for preventative maintenance that minimizes downtime.
AI also excels in predictive analytics. By analyzing historical data, AI can forecast demand for specific products, enabling manufacturers to adjust production schedules accordingly. This ensures they can meet customer demand without overproducing, further reducing waste and costs.
Spotlight on Svegea’s AI-Integrated Textile Machines
Svegea of Sweden is a leading innovator in the textile machinery industry, known for its commitment to quality and efficiency. One standout product is the EC 300 Collarette Cutter, an AI-integrated machine that exemplifies the benefits of modern technology in textile manufacturing.
The EC 300 optimizes the cutting process, ensuring precision and consistency with every cut. With AI at its core, the machine can analyze fabric and make real-time adjustments to cutting parameters, reducing waste and enhancing efficiency. The result is a product that meets and exceeds the high standards expected by today’s manufacturers.
Svegea’s commitment to innovation extends beyond this. The company continuously invests in research and development, ensuring its machines remain at the cutting edge of technology. By integrating AI into its products, Svegea leads the charge toward a more efficient, sustainable, and productive textile industry.
To learn more about Svegea’s AI-integrated textile machines, talk to us now!